Про Егорьевскую обувную фабрику
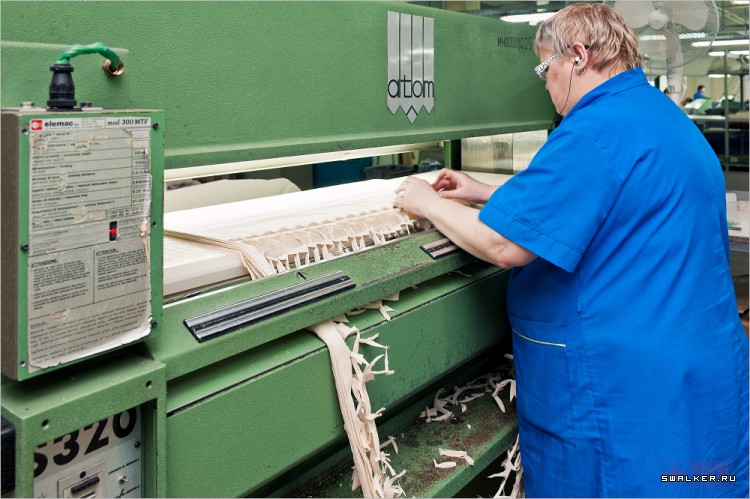
Итальянский пресс для вырубки.
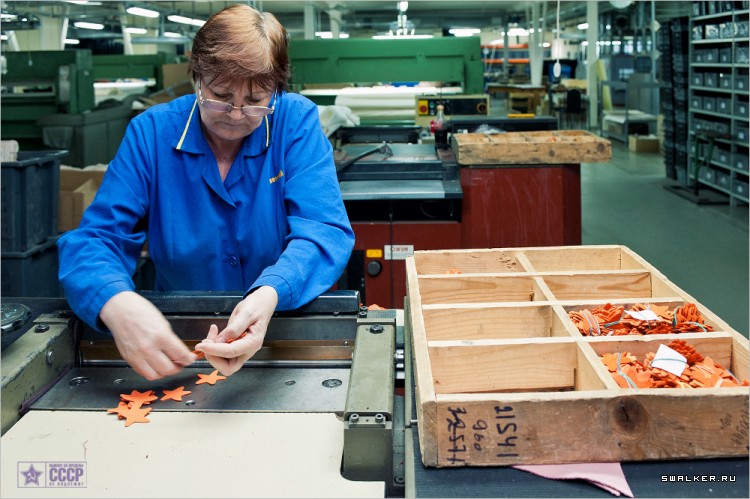
Работа с фигурными деталями, предназначенными для декорирования обуви.
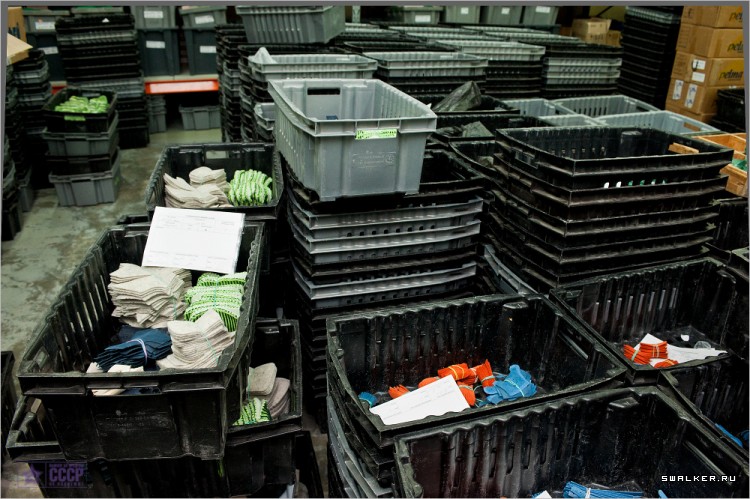
После завершения процесса раскроя и вырубки деталей, они комплектами поступают в комплектовочную. Там всё раскладывается по таким ящикам с приложением сопроводительного талона.
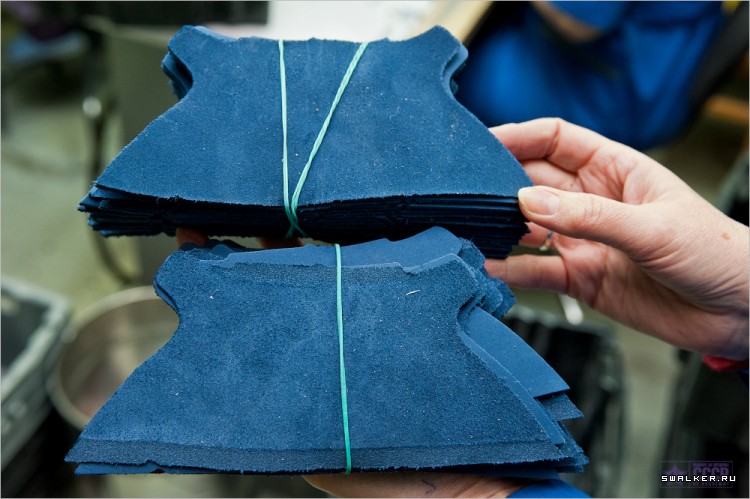
Часть уже скомплектованных деталей нуждается в дополнительной специальной обработке. Сверху — ещё необработанная деталь, снизу — обработанная, со сточенными краями. Обработка важна для последующей подгонки ровного шва.
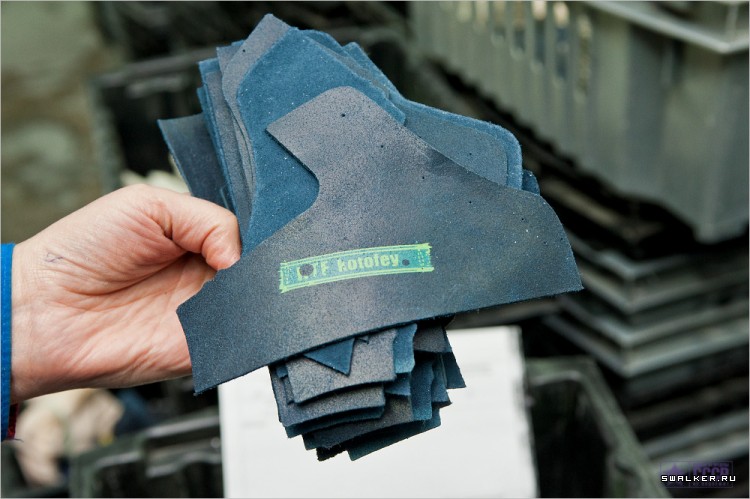
Часть деталей отправляется на принт, вышивку, термоаппликацию или шелкографию.
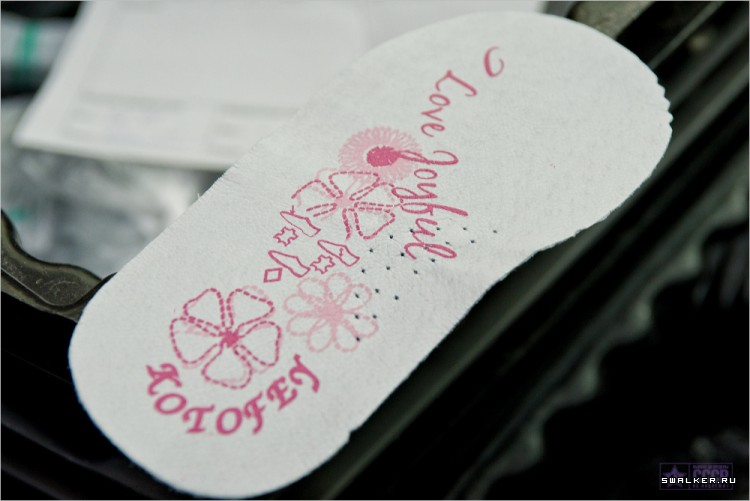
Помимо декоративного рисунка, на стельку нанесена информация, стандартно требуемая от производителя: материалы верха, подкладки и низа.
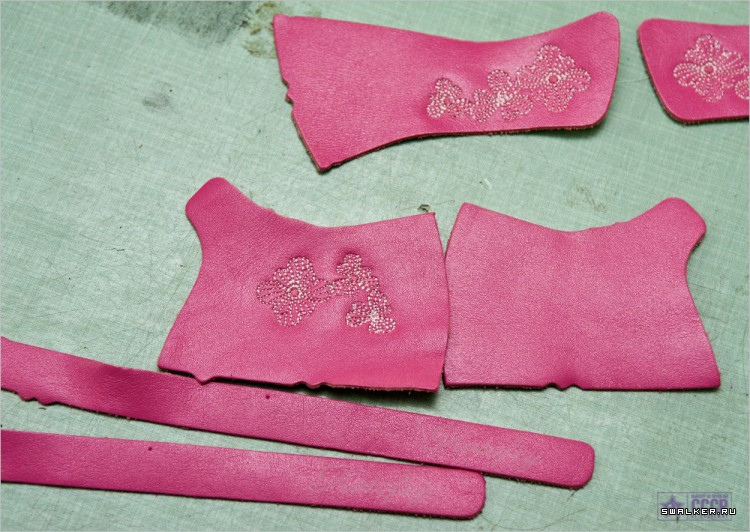
Рисунок или текст, размещаемый на деталях, продумывается модельерами на этапе создания проекта модели обуви. Обратите внимание на микровырезы и наколы, видимые на заготовках. Они послужат ориентиром и точно укажут откуда начинать ведение строчки при сшивании деталей.
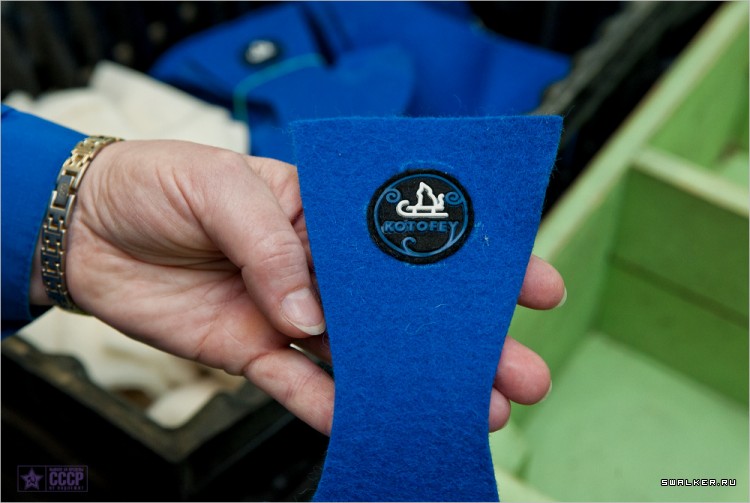
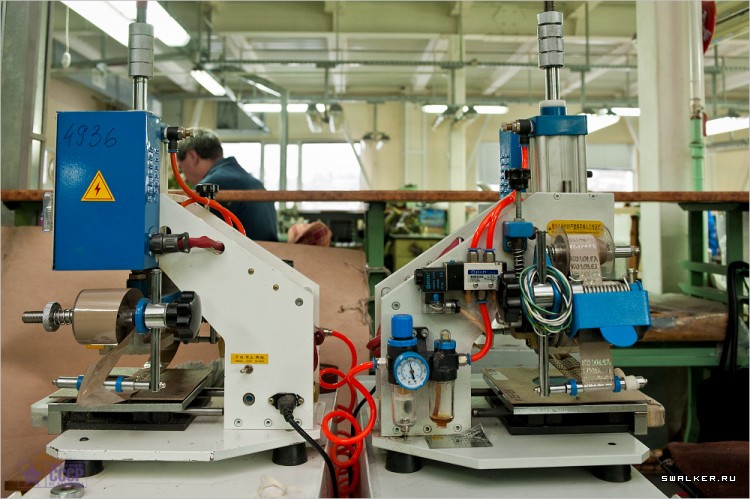
Китайское оборудование для отделочных операций.
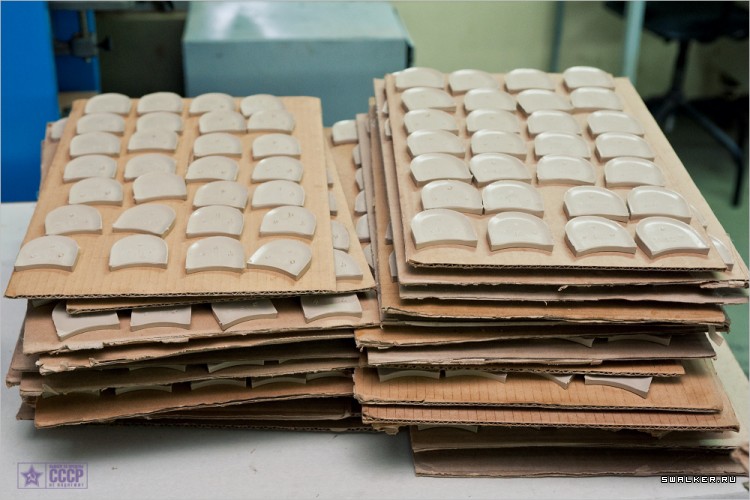
Детские каблучки. Привозные. Отечественные.
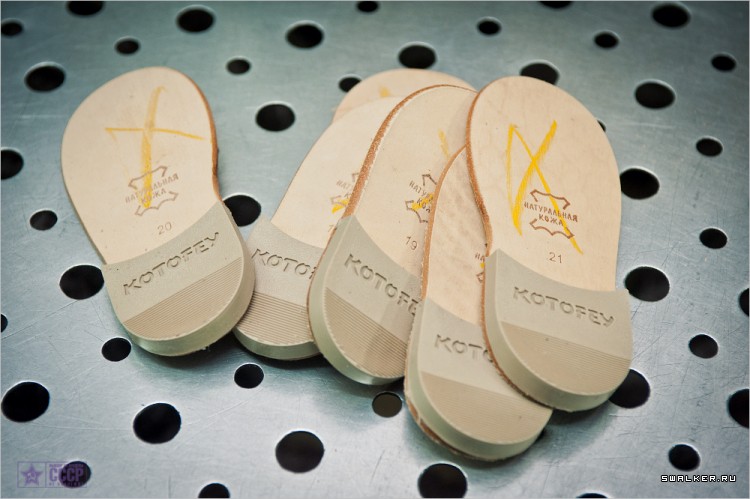
Чепрачная кожа в листах на фабрике подвергается дополнительной обработке: её прессуют, выравнивают, рубят на подошвы, вырубку фрезеруют по периметру, приклеивают каблук, подгоняют одно к другому и часть полученного полуфабриката… бракуют. Пример на фото.
Всё, что даже в небольшой степени не соответствует стандартам — отбраковывается. Каблук в таком случае могут оторвать и заново запустить в производство, а вот с чепраком подобный номер невозможен. Сделать из подошвы бОльшего размера подошву меньшего можно. Особенно, если бракованный участок пришёлся на край и может быть безболезненно отрезан. Но нецелесообразно. Переклеймить размер на обрезанной подошве получается уже дороже.
Каблук на обуви для малышей нужен не для красоты, а для безопасности. Он помогает правильно сформироваться детской стопе и, если уж ребёнку случится упасть, то сделать он это должен в направлении «вперёд», а не «назад». Такое падение для ребёнка гораздо безопаснее.
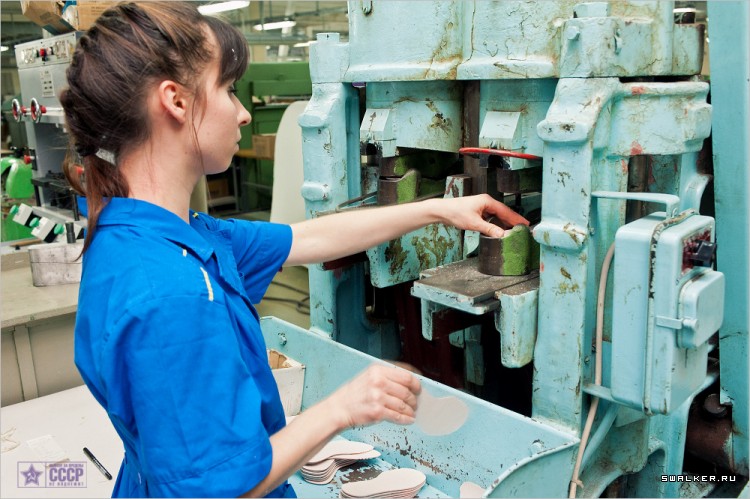
Процесс формовки стельки. На специальную колодку укладывают плоскую заготовку, прижимают матрицей к колодке и получают готовый стелечный узел: сформованную 3D-стельку, склеенную с полустелькой.
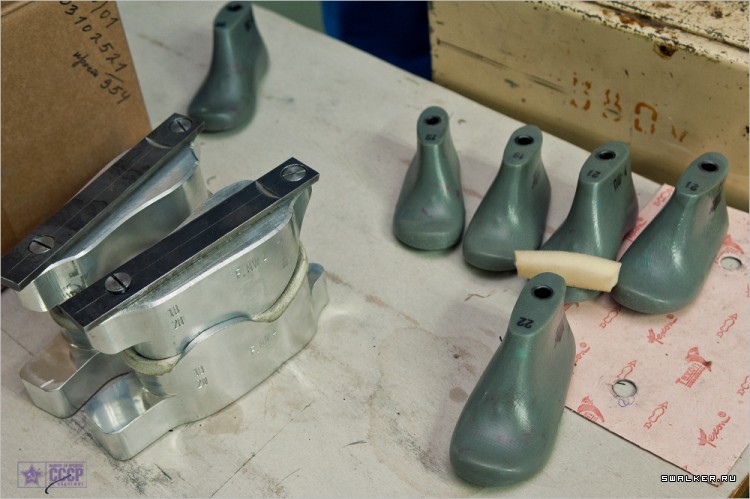
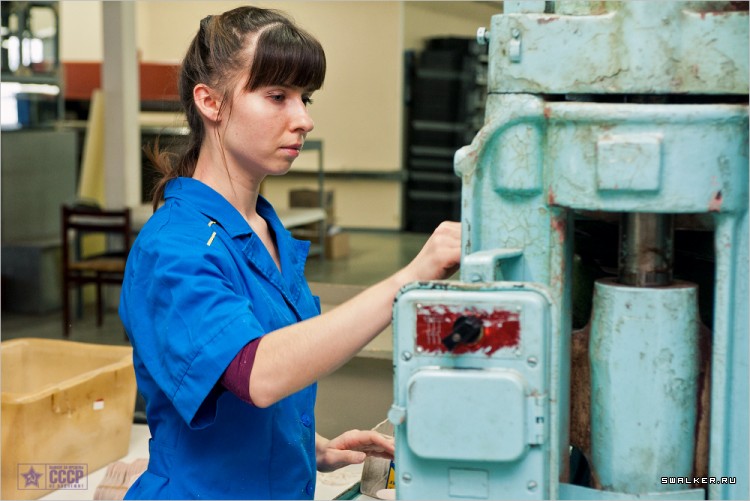
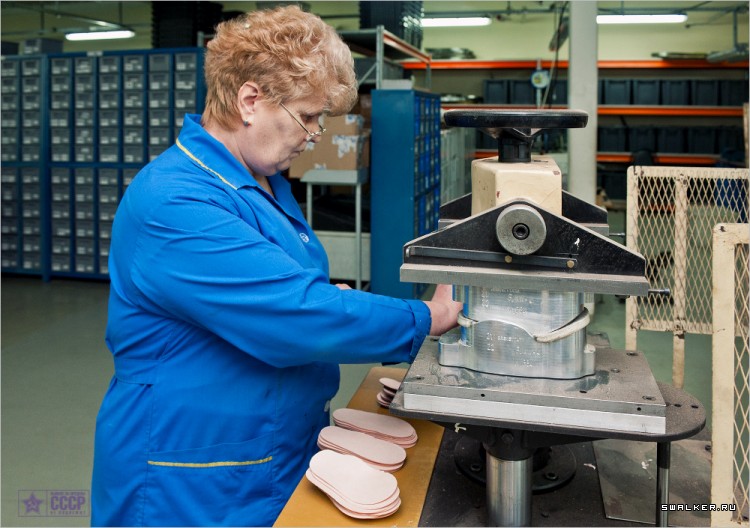
Часть стелек не формуется совсем, например, стельки для босоножек. Надобности нет.
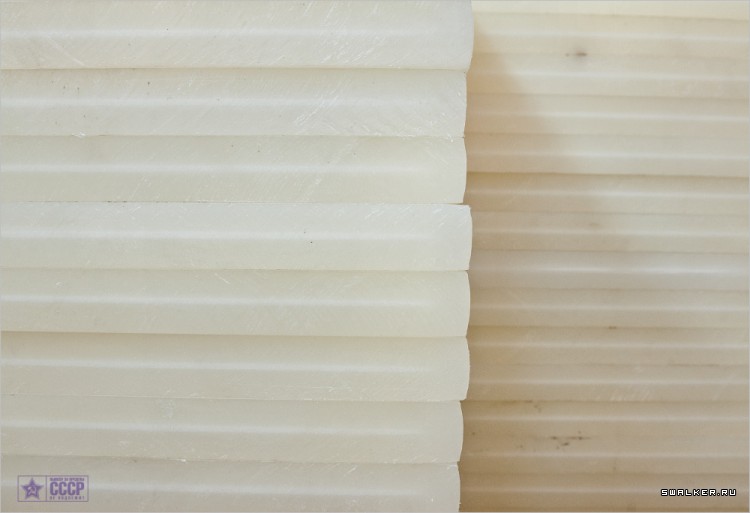
Перед нами полиэтиленовая вырубочная плита. Именно на неё приходится удар резака.
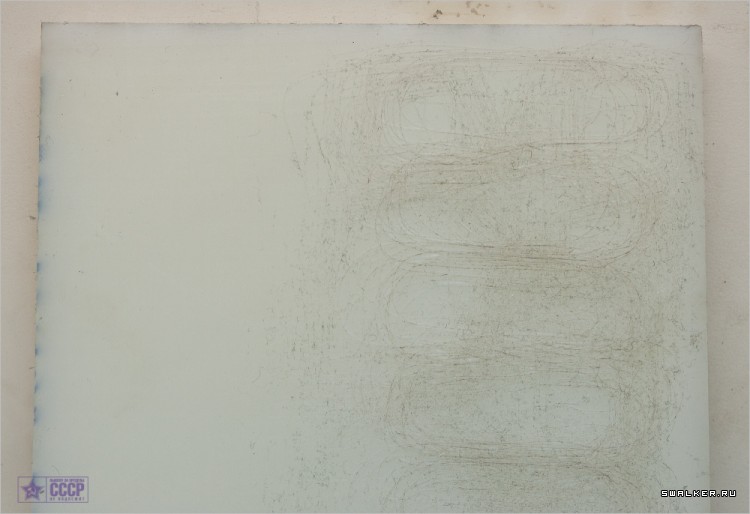
Со временем плита приходит в негодность и отправляется в спецмашину, состругивающую шершавый слой.
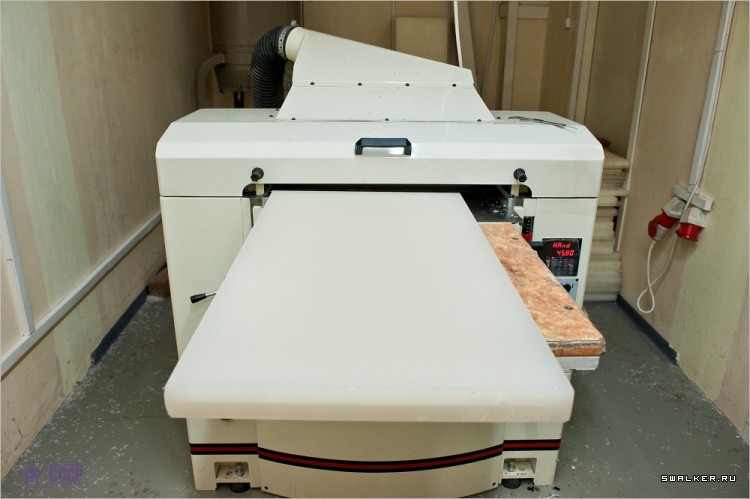
Реанимация изношенной плиты.
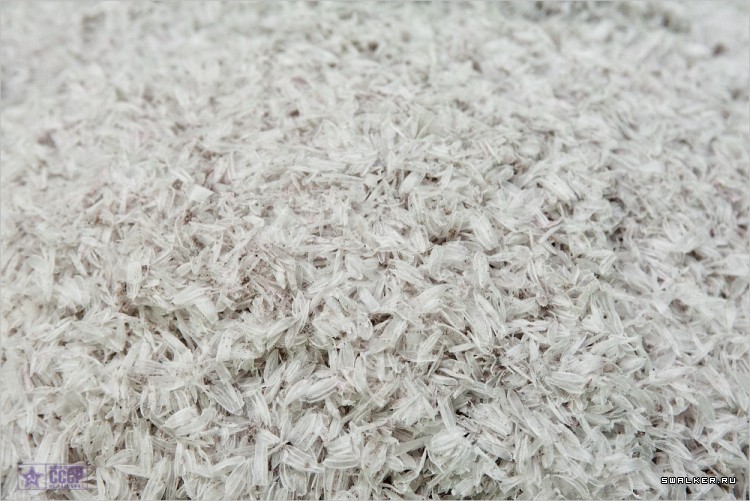
Плиточная стружка.
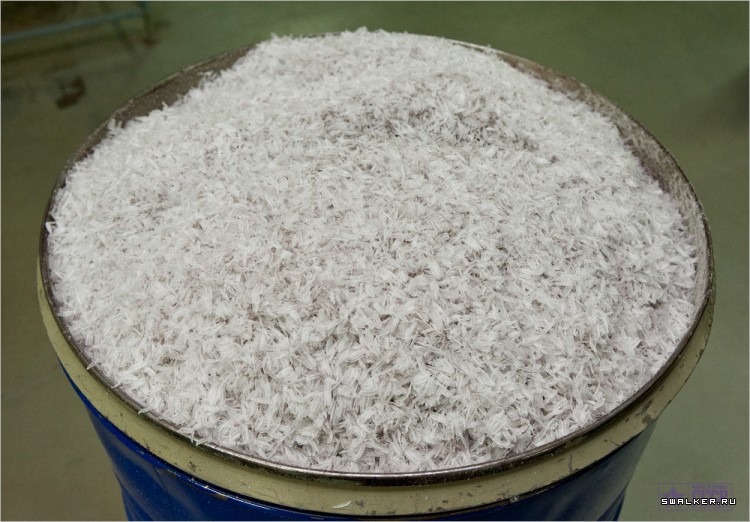
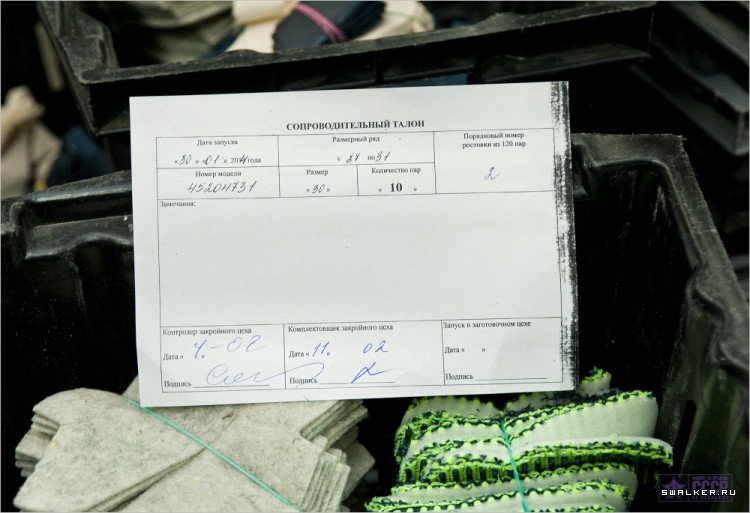
Партия деталей, полученная от закройщиков, обработанная, скомплектованная и снабжённая сопроводительными документами готовится к сдаче в заготовочный цех. Стандартный размер сдаваемой партии — 960 пар. Вслед за комплектами деталей отправляемся из закройного цеха в заготовочный.
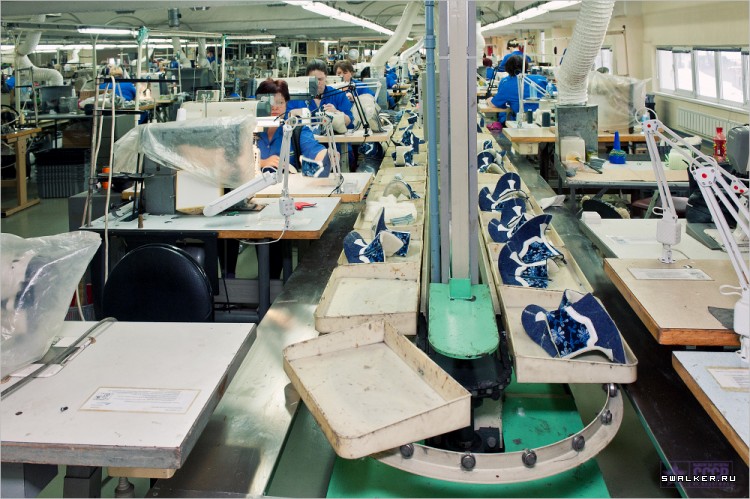
В заготовочном цеху собирается из деталей верх обуви. Производство конвейерное. Большинство машин снабжено подвижными платформами, позволяющими передвигать машины к любому месту в меняющейся технологической цепочке.
Скорость движения конвейера изменяют, руководствуясь плановым заданием и текущей производительностью труда. Весь цех — 102 работника. Конвейер в среднем требует участия около 30 человек на модель.
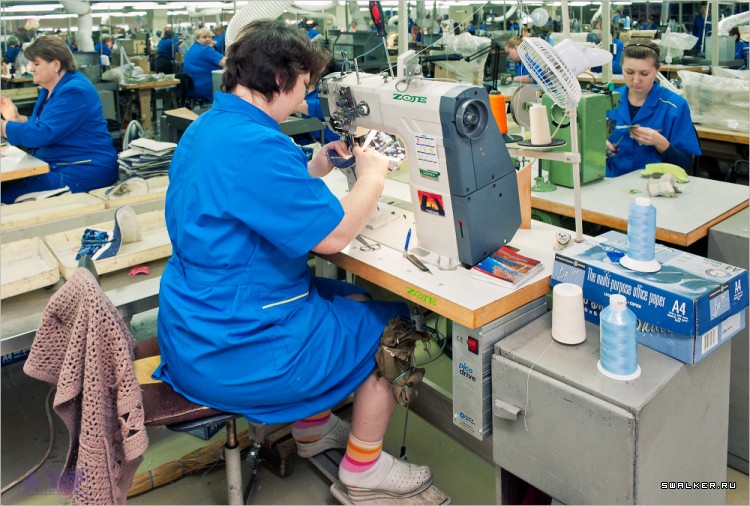
Комплект деталей складывается в лоток и отправляется «по инстанциям». Работа в цеху довольно однообразная и требующая изрядного внимания. Молодёжи за швейными машинами мало, та предпочитает сидение в офисных креслах.
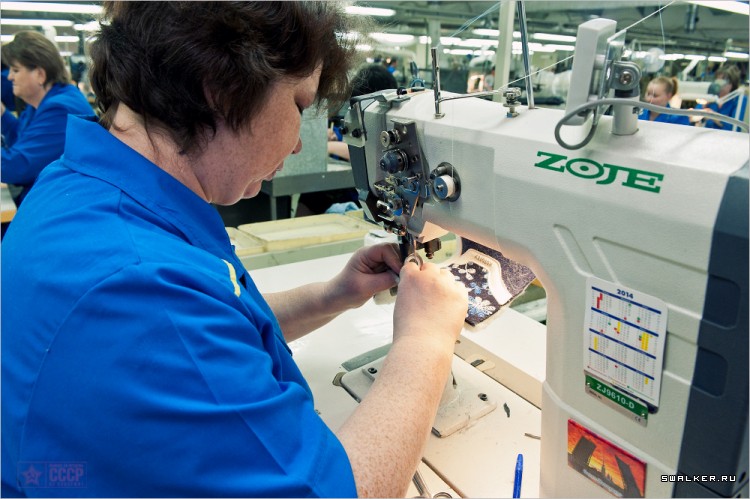
Детали сшиваются между собой по тем самым микрознакам и предварительно сделанным наколам. На каждом этапе конвейера швея выполняет свою технологическую операцию. Например, разглаживает шов и нашивает на него тесьму, чтобы ногу внутри обуви ничто не царапало и не раздражало.
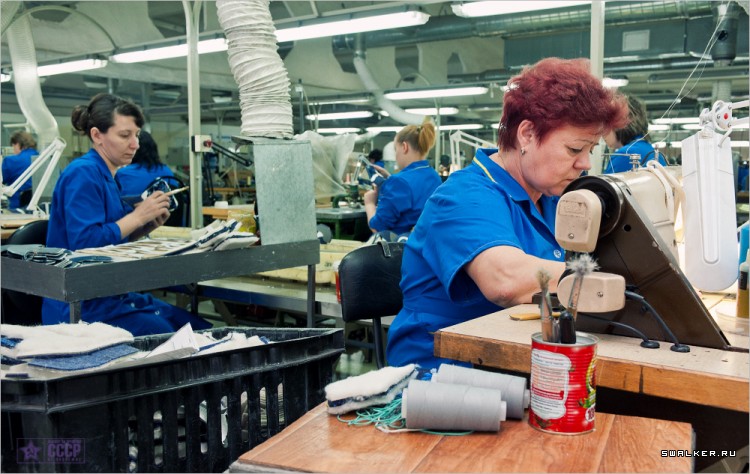
Часть деталей нашивается одна на другую, часть требует стачивания — пришивания встык зигзагообразным швом. Операция требующая аккуратности, кожа — не ткань, повторной прошивки не потерпит.
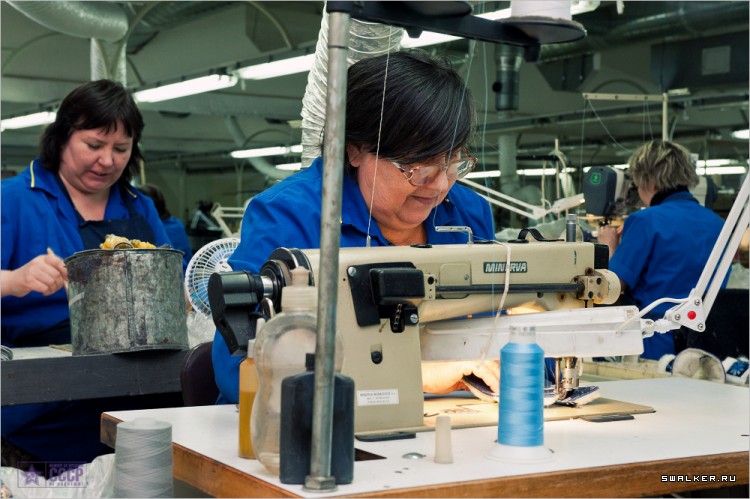
К состроченной детали пришиваем элемент фурнитуры — рамку, куда будет продет ремень-застёжка. Сам элемент перед пришиванием надо собрать вручную. Автоматизировать подобные операции человечество пока не научилось.
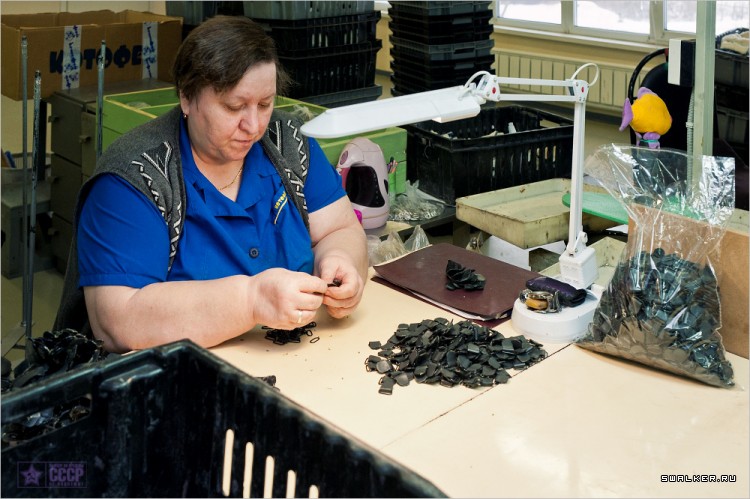
Люди на конвейере могут меняются в рамках своей квалификации.

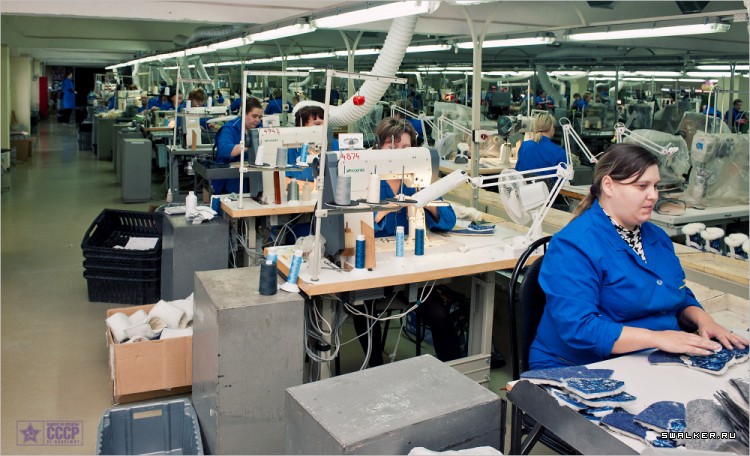
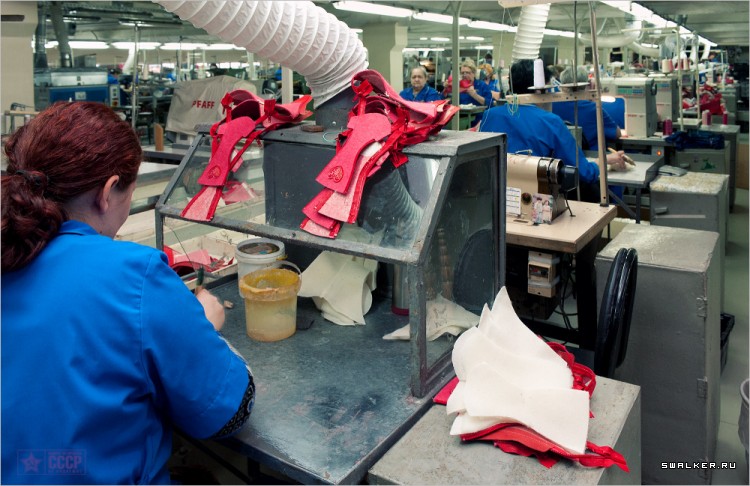
Заготовка, проходя по конвейеру, начинает напоминать готовый продукт.
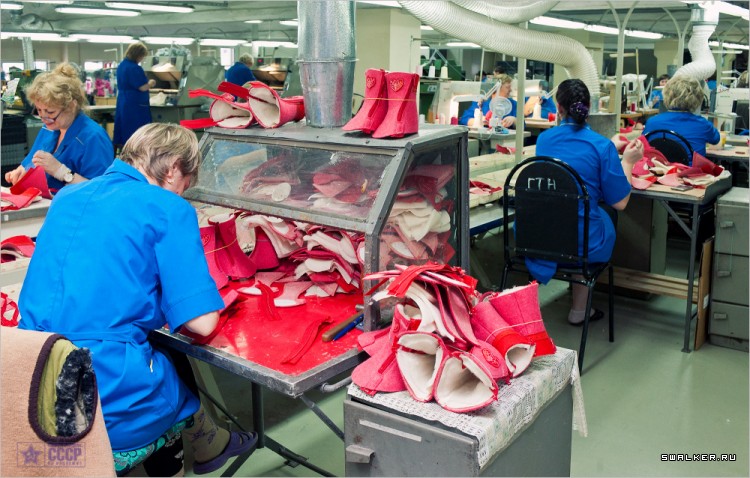
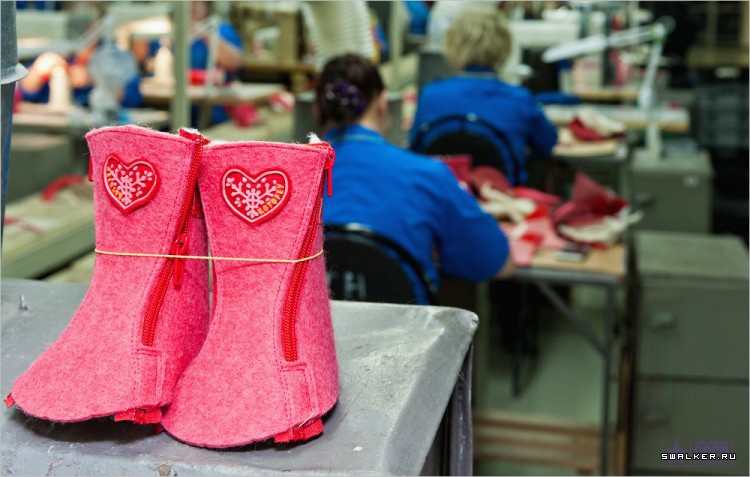
Детский войлочный сапог. В Егорьевске этот класс продукции «возрождён» в начале двухтысячных.
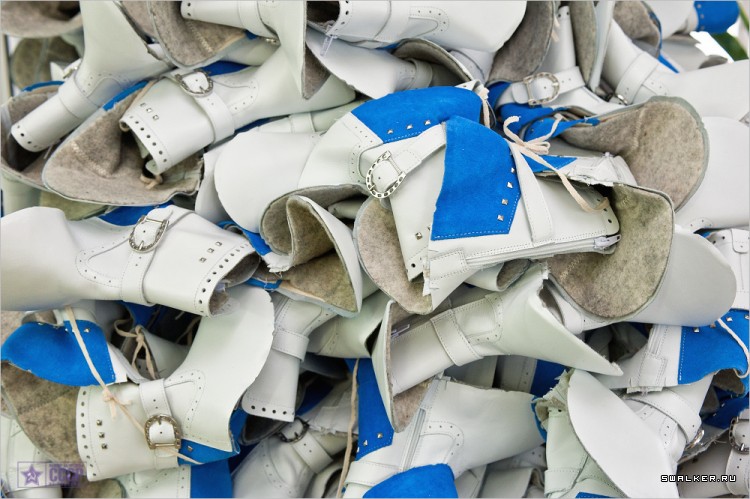
Почти готовый верх обуви.
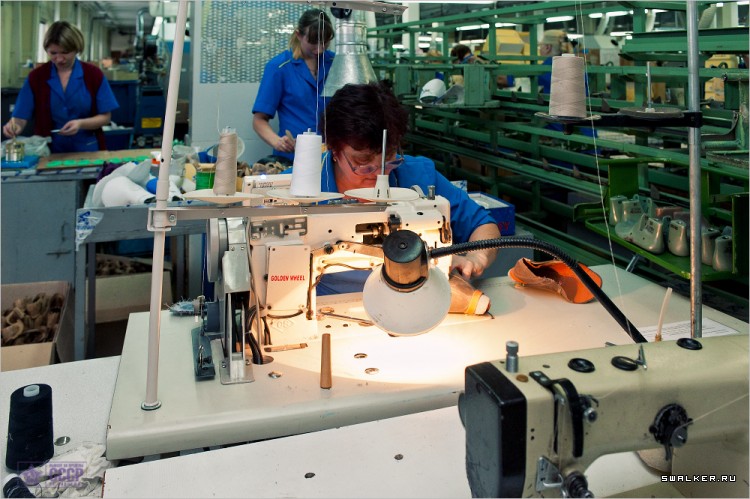
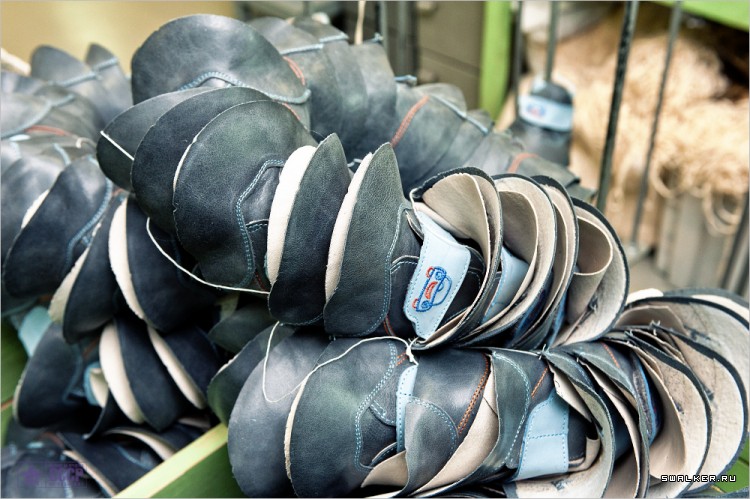
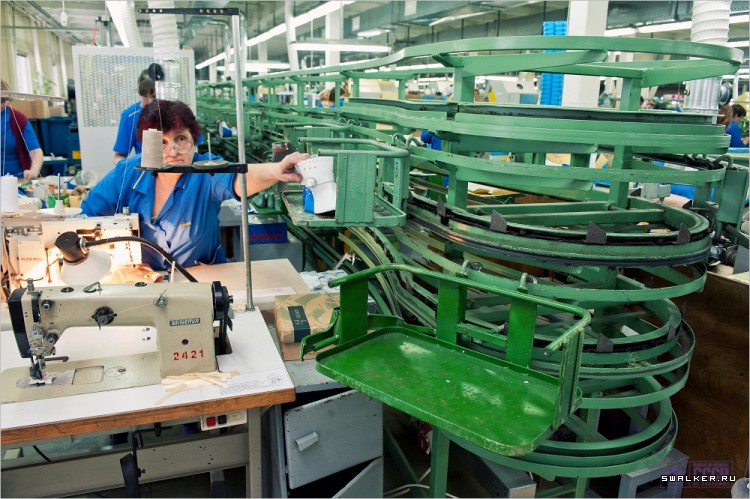
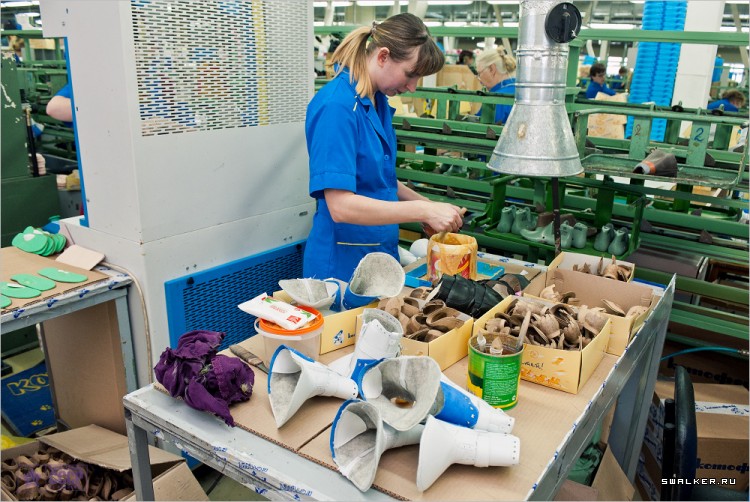
Вклейка жёсткого задника.
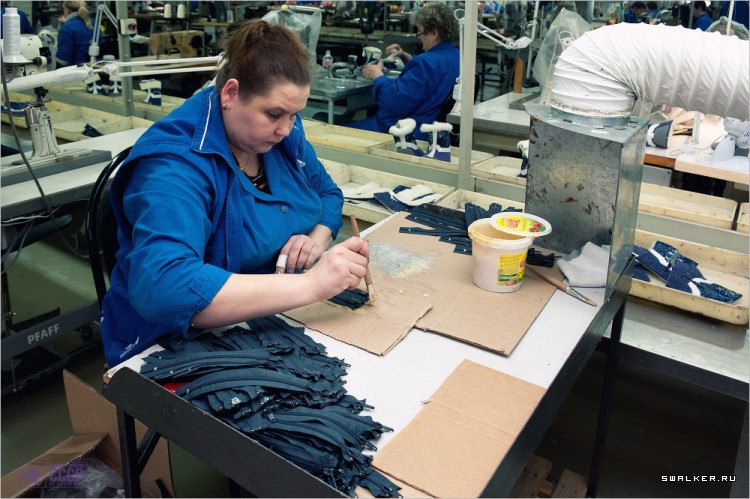
К детали приклеивается застёжка-молния. На следующем этапе молнию пришьют, а приклеивание позволяет освободить швее руки и избежать перекосов при подаче деталей под строчку.

Без паяльника в обувном деле никак не обойтись.
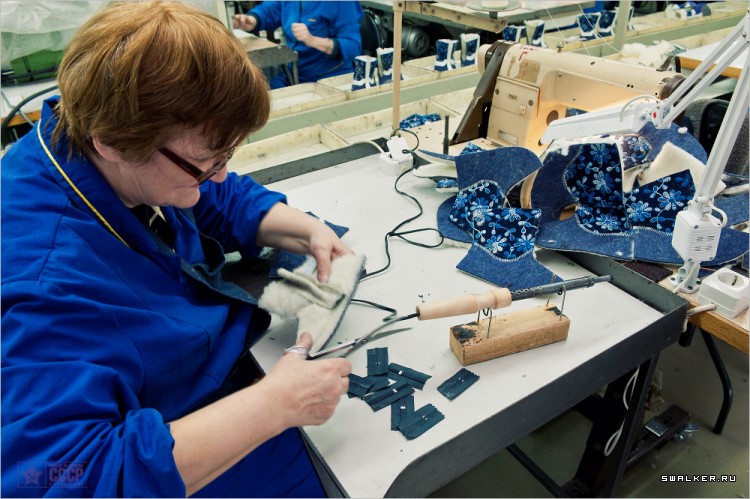
Приклеенная, а затем и пришитая к заготовке застёжка-молния обычно длиннее, чем нужно. Лишнее вручную отрезается ножницами.
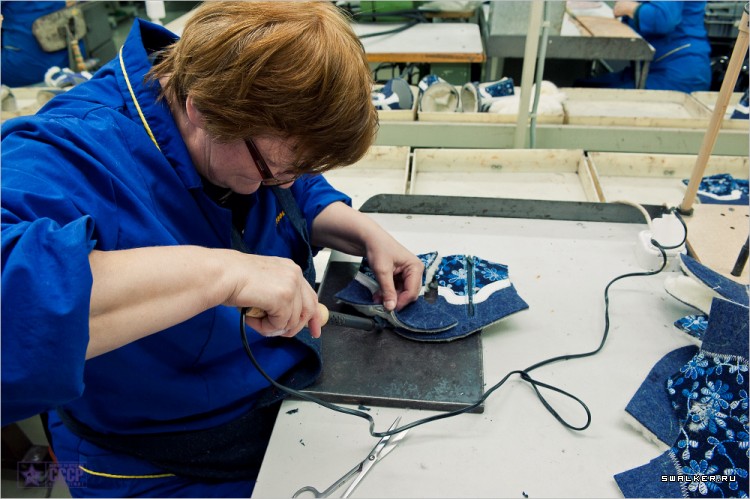
Затем вручную запаивается паяльником.
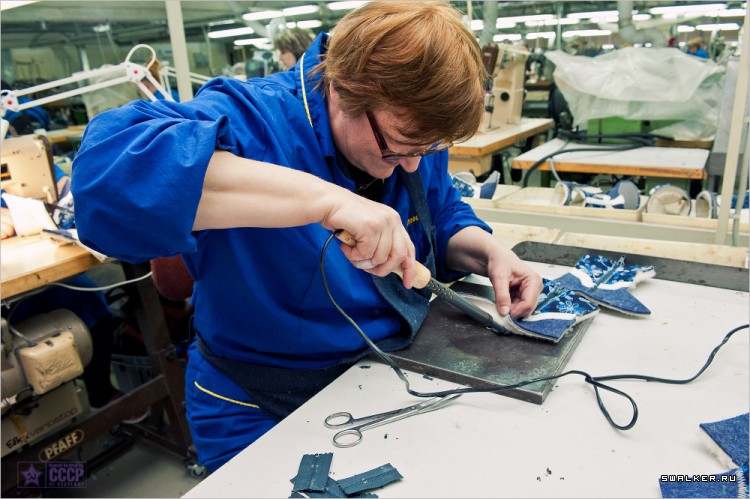
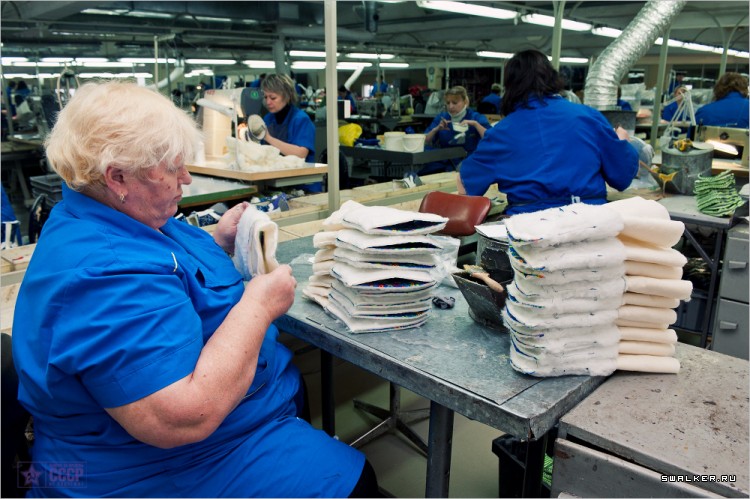
Как и молнию, клеем промазывают верх и подкладку.
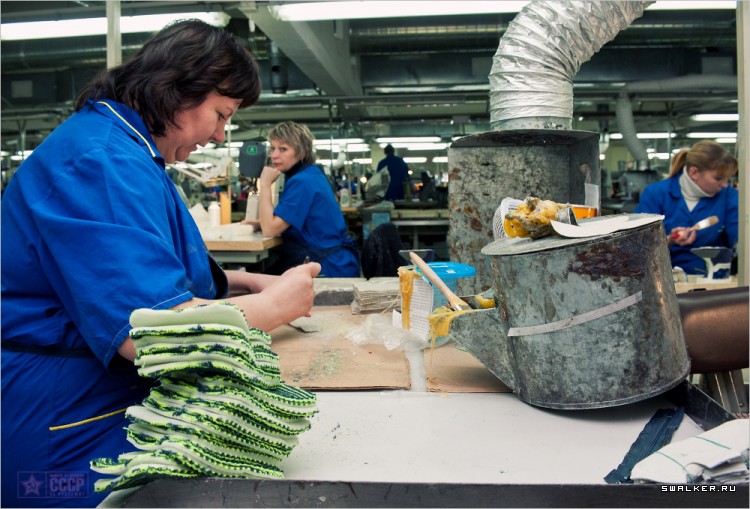
Есть в процессе склеивания некоторые технологические хитрости. Например, детали нельзя сразу же прижимать друг к другу. Потому операции на конвейере разнесены таким образом, чтобы минуты, необходимые для надёжного склеивания, прошли естественным образом, не тормозя всего производства.
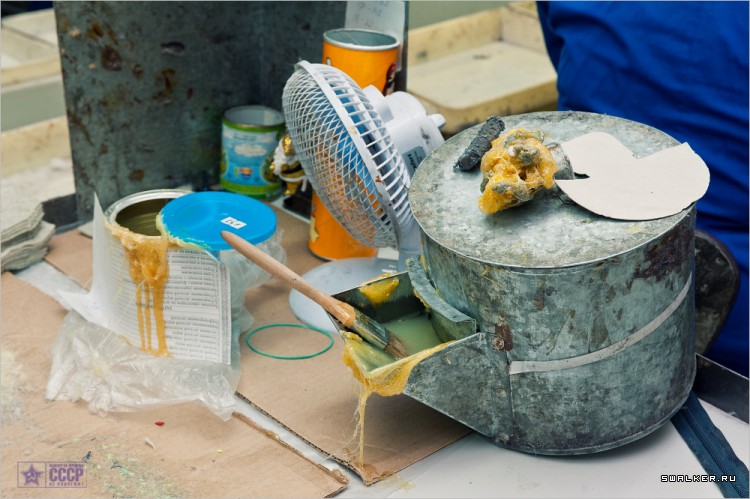
Чтобы склеиваемые поверхности плотно прилегали друг к другу, заготовка, промазанная клеем, попадает под специнструмент.
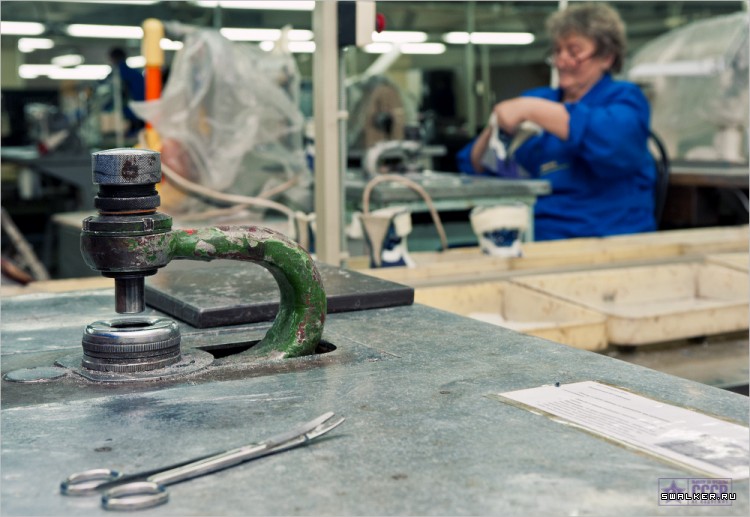
Инструмент называется «околачивателем». С большой частотой и небольшим усилием он «приколачивает» детали друг к другу, гарантируя надёжность склейки. Одна из немногих операций, с которой справились бы даже некоторые фотографы. Ну, процент способных к этому делу среди никонистов, думаю, повыше будет.
Уточнил статистику травматизма в рядах операторов околачивателя. Засунуть в аппарат палец возможным не представляется, он туда не пролезет. Но если стараться специально — можно прищемить. Проверять не стал.
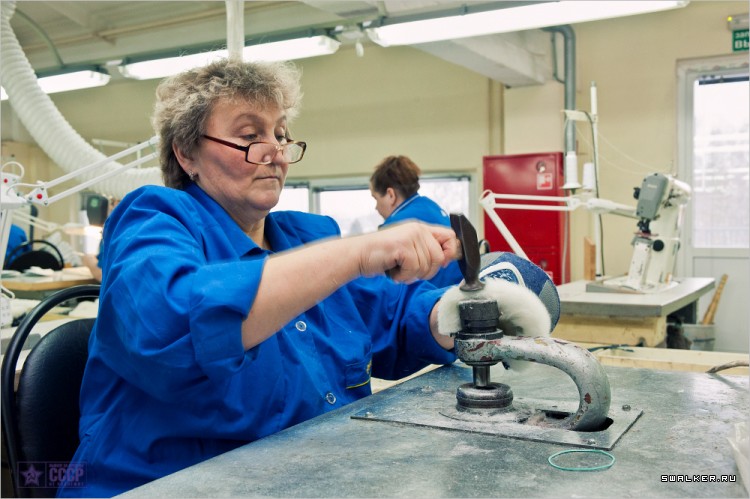
Иногда околачивают вручную, например, в случае с опушкой. Ещё одна операция, выполняемая всегда только вручную — обрезка излишков кожподкладки с заготовки. Автоматизировать её нельзя в принципе.
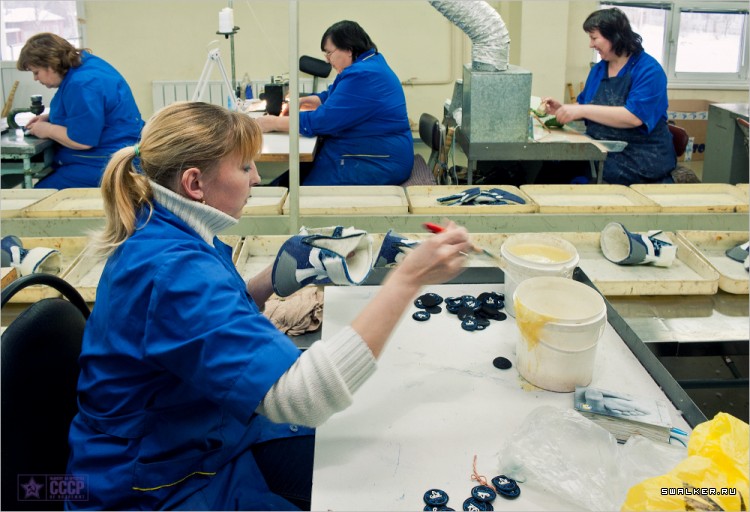
Приклеивание декоративного элемента. Обратите внимание на клапан, вшитый в сапожок. Даже если застёжка у ребёнка случайно расстегнётся — снег в сапог не попадёт и детские ноги останутся сухими и тёплыми.

Чтобы носок ботинка держал форму и не деформировался, к нему приклеивается подносок из тонкого термопластичного материала. Пришивать его нельзя, это тонкий пластик.
Подобная история происходит и с задником. По ГОСТу, до определённого размера, детскую обувь без жесткого задника выпускать просто нельзя.
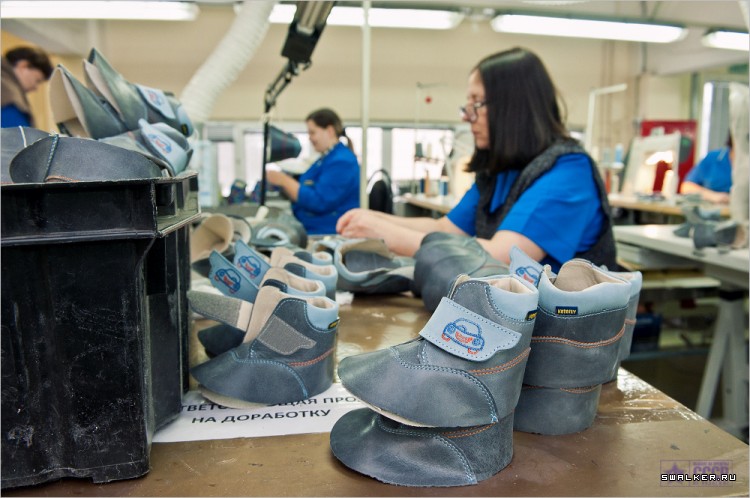
Вот и конец технологической цепочки. Пристрачивание элементов отделки и контроль качества. Ботинок или сапожок уже вполне узнаваемы
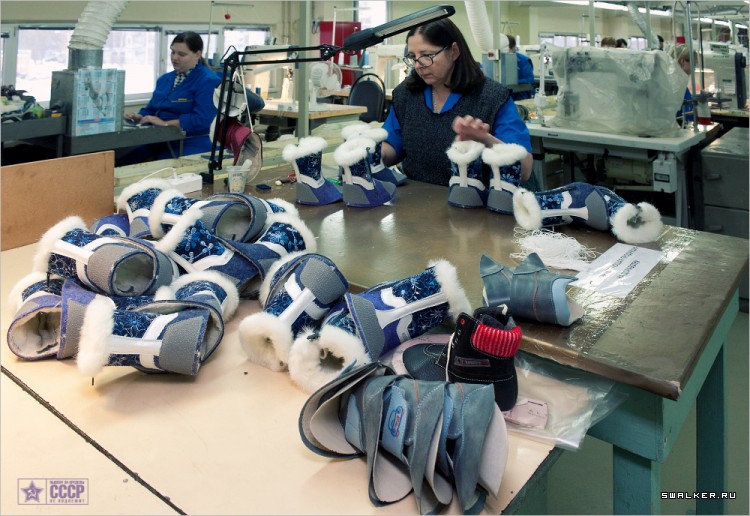
Работа на производстве непростая, в связи с отсутствием готовых кадров, их готовят прямо на производстве из числа желающих. На фабрике нет и в помине засилья т.н. «гастарбайтеров». Учитывая общую депрессивность отрасли — шаг, безусловно, серьёзный.
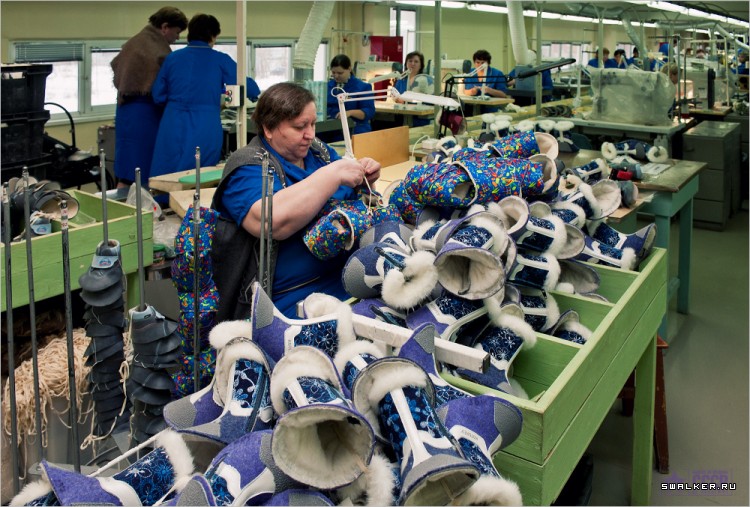
Скомплектованные по размерам заготовки собираются в пары. Распаривание заготовок на любых этапах не приветствуется, даже небольшие расхождения, например, в оттенке материалов, могут привести к расстройству покупателя и отказу от покупки.
Обратите внимание на верх сапожка из итальянского красивого войлока, низ из отечественного тёплого и непродуваемого войлока и искуственный мех. Такой мех делают из натуральной шерсти на текстильной основе. Всё вместе получается красивым, надёжным и тёплым одновременно.
Комментарии - всего 4