Про Егорьевскую обувную фабрику
Экскурсия в производственные цеха ОАО Егорьевск-обувь, Московская область, февраль 2014г.
Осенью 1935 года в помещении бывшей фабрики-кухни города Егорьевска (Московская область) было демонтировано оборудование и начались работы по переустройству здания под промышленное предприятие. В 1936 году фабрика была принята к эксплуатации и приступила к выпуску детской обуви. Сегодня обувное производство в Егорьевске не без успеха продолжают. Всем желающим предлагается пройтись по фабричным цехам и понаблюдать за процессом создания отечественной детской обуви, выпускаемой под торговой маркой «Котофей». Автор материала Михаил Михин
Сложно сказать, с чего именно начинается производство обуви. Легко сказать без чего обувь сделать не получится вовсе: без колодок и штампов-резаков. Вот с них и начнём.
![Про Егорьевскую обувную фабрику Про Егорьевскую обувную фабрику]()
РМЦ — ремонтно-механический цех. Заготовки будущей обувной колодки. Были внезапно приняты за заготовки для деталей пулемёта РПК.
![Про Егорьевскую обувную фабрику Про Егорьевскую обувную фабрику]()
Заготовка попадает в копировальный станок.
![Про Егорьевскую обувную фабрику Про Егорьевскую обувную фабрику]()
Станок вытачивает копию колодки, ориентируясь на «мастер-модель». Похожим образом в бытовых мастерских изготавливаются копии ключей.
![Про Егорьевскую обувную фабрику Про Егорьевскую обувную фабрику]()
![Про Егорьевскую обувную фабрику Про Егорьевскую обувную фабрику]()
Доведённая до пригодного состояния колодка отправляется на производство.
![Про Егорьевскую обувную фабрику Про Егорьевскую обувную фабрику]()
Такие колодки изготавливаются для каждого размера. Создание мастер-колодки, с которой делаются копии — высший пилотаж обувного производства. Мастер-колодочник должен учесть массу нюансов, в том числе возрастных и национальных. Русская нога — это всегда «кого надо нога». Наша национальная особенность — высокий подъём, и у детей и у взрослых. Русская детская нога пошире других, узкие европейские колодки для нас не подходят.
В середине двухтысячных на фабрике целый год велась работа по созданию новой колодки для обуви ясельной и малодетской групп. Пять сотен детей обмеряли и проанализировали итоги, собрали статистику по полноте, подъёму, высоте каблука. Новые колодки позволили начать выпуск по-настоящему удобной, эргономичной и ортопедически правильной обуви, что важно именно для растущей детской стопы.
С колодки начинается и всякая новая обувь. На этапе конструирования с колодки и присовокупленной подошвы снимается чертёж-полуразвёртка, оцифровывается и поступает в компьютер. Где обрабатывается дизайнерами и технологами в автоматизированной системе конструирования обуви. В дальнейшем тестовая модель производится в единичном экземпляре и отправляется на рассмотрение худсовета. Будучи утверждённой, модель поступает в массовое производство. На утверждённую модель создаётся модельный паспорт, где подробно и детально описывается всё, касающееся материалов и технологии производства модели.
Казалось бы, что может быть проще ботинка? Ан, нет. Не революционные, конечно, перевороты, но новые, свежие конструктивные решения постоянно находятся. А вот специалисты в этой области находятся не так часто, разрыв между наукой и производством в отечественной лёгкой промышленности растёт всё сильнее. Удивительного ничего нет: сельское хозяйство и лёгкая промышленность сейчас в категории сильно отстающих, в частности, по зарплатам. Второй непривлекательный аспект — и там и там надо работать. Такое не всем нравится.
![Про Егорьевскую обувную фабрику Про Егорьевскую обувную фабрику]()
Колодка сделана, модель определена, дело за материалами.
![Про Егорьевскую обувную фабрику Про Егорьевскую обувную фабрику]()
Для каждой модели технологически важно выбрать необходимые материалы. Крепкие нитки, например.
Неплохое турецкое название. Запоминающееся.
![Про Егорьевскую обувную фабрику Про Егорьевскую обувную фабрику]()
![Про Егорьевскую обувную фабрику Про Егорьевскую обувную фабрику]()
![Про Егорьевскую обувную фабрику Про Егорьевскую обувную фабрику]()
![Про Егорьевскую обувную фабрику Про Егорьевскую обувную фабрику]()
![Про Егорьевскую обувную фабрику Про Егорьевскую обувную фабрику]()
![Про Егорьевскую обувную фабрику Про Егорьевскую обувную фабрику]()
Необходимые натуральные и синтетические материалы, нитки, фурнитура — всё готово к началу производства. Но начать его без штампов нельзя.
![Про Егорьевскую обувную фабрику Про Егорьевскую обувную фабрику]()
Штампы-резаки для обувной промышленности изготавливаются работниками РМЦ — ремонтно-механического цеха.
![Про Егорьевскую обувную фабрику Про Егорьевскую обувную фабрику]()
Бухта со специальной резачной сталью.
![Про Егорьевскую обувную фабрику Про Егорьевскую обувную фабрику]()
![Про Егорьевскую обувную фабрику Про Егорьевскую обувную фабрику]()
![Про Егорьевскую обувную фабрику Про Егорьевскую обувную фабрику]()
![Про Егорьевскую обувную фабрику Про Егорьевскую обувную фабрику]()
![Про Егорьевскую обувную фабрику Про Егорьевскую обувную фабрику]()
![Про Егорьевскую обувную фабрику Про Егорьевскую обувную фабрику]()
![Про Егорьевскую обувную фабрику Про Егорьевскую обувную фабрику]()
После довольно прецизионного формования будущего резака он сваривается и затачивается.
![Про Егорьевскую обувную фабрику Про Егорьевскую обувную фабрику]()
![Про Егорьевскую обувную фабрику Про Егорьевскую обувную фабрику]()
![Про Егорьевскую обувную фабрику Про Егорьевскую обувную фабрику]()
![Про Егорьевскую обувную фабрику Про Егорьевскую обувную фабрику]()
Комплект резаков для производства одной модели обуви.
![Про Егорьевскую обувную фабрику Про Егорьевскую обувную фабрику]()
Помимо штампов-резаков, в производстве обуви применяются и более нежные инструменты.
![Про Егорьевскую обувную фабрику Про Егорьевскую обувную фабрику]()
Исключительной ценности (во всех смыслах) предметы — резаки отделки. Сделаны в Италии. Каждый пронумерован. Раньше резаки на фабрике делали самостоятельно, это было и сложно и дорого. Теперь предпочитают использовать итальянские, как более качественные и доступные по цене.
![Про Егорьевскую обувную фабрику Про Егорьевскую обувную фабрику]()
Внутри резака находится упругий материал, автоматически выталкивающий свежевырубленную деталь.
![Про Егорьевскую обувную фабрику Про Егорьевскую обувную фабрику]()
Резаки. Те самые, что поступают готовыми наборами из РМЦ. В процессе производства резаки могут подтупиться. Механики их поправят, подточат и снова вернут на производственный участок. Совсем изношенные резаки будут заменены новыми.
![Про Егорьевскую обувную фабрику Про Егорьевскую обувную фабрику]()
Хранят резаки в спецшкафах. На каждой ячейке указан номер модели, а специальный код разъяснит в каком ряду и на какой полке находятся резаки для данной конкретной модели.
![Про Егорьевскую обувную фабрику Про Егорьевскую обувную фабрику]()
К каждому размеру каждой модели готовят свой комплект резаков.
![Про Егорьевскую обувную фабрику Про Егорьевскую обувную фабрику]()
Всё это хозяйство хранится в закройно-штамповочном цеху.
![Про Егорьевскую обувную фабрику Про Егорьевскую обувную фабрику]()
Цех состоит из двух участков: закройного (раскрой верха обуви, межподкладки и подкладки; используются кожевенные и текстильные материалы, мех, войлок) и штамповочного. На последнем производятся раскрой и обработка деталей низа. Среди таковых замечены: основная стелька, полустелька, стелечный узел (склеенные между собой стелька и полустелька) и подошва из чепрака.
Любая обувь, и взрослая и детская, состоит из приличного количества деталей. Если мысленно разобрать обычный ботинок на составляющие, то можно насчитать до 80 деталей.
Особенность производства детской обуви — исключительная требовательность к соблюдению размеров. Если на взрослой обуви погрешность в пару миллиметров может остаться незамеченной, то на детской ноге такая погрешность недопустима. Это обстоятельство учитывают везде, начиная с производства резака.
![Про Егорьевскую обувную фабрику Про Егорьевскую обувную фабрику]()
Растянутый на спецвалике материал называется термином «кожевенный товар», а среди работников именуется просто «товаром». Здесь, в самом начале производственного цикла, «товар» внимательно осматривают, помечая сомнительные в смысле качества участки каким-нибудь значком. При раскрое «товара» помеченные участки будут закройщиком опознаны как непригодные и в дело не пойдут.
![Про Егорьевскую обувную фабрику Про Егорьевскую обувную фабрику]()
Из «товара» формируется заказ, к которому прилагается раскройная карта.
![Про Егорьевскую обувную фабрику Про Егорьевскую обувную фабрику]()
Типичный представитель «товара». Наверху наш, отечественный войлок. Ниже китайская ткань, в самом низу совместное российско-итальянское творчество. Отечественных материалов в обувном производстве немного. Российские поставщики сырья, в лучшем случае, остановились в технологическом развитии на уровне позднего СССР, а в худшем вовсе прекратили своё существование.
![Про Егорьевскую обувную фабрику Про Егорьевскую обувную фабрику]()
Это итальянский войлок. Красивый внешне и дублированный мехом изнутри. По качеству наш войлок лучше, плотнее. Итальянский заметно рыхлее, хуже теплоизолирует, зато выглядит наряднее. Приходится либо дополнительно украшать наше сырьё, либо использовать итальянский товар, привлекательный прямо из рулона. Такая же петрушка и с фурнитурой: отечественных комплектующих мало или нет совсем, приходится закупать иностранные. Хотя фурнитуру можно производить и самостоятельно, это совсем не rocket science.
![Про Егорьевскую обувную фабрику Про Егорьевскую обувную фабрику]()
Интересная ситуация складывается с кожсырьём. Выгодно проделать разного рода «грязные» операции по первичной обработке кожи здесь, потом отправить её за рубеж, там отделать и продать по совсем уже другой цене обратно.
![Про Егорьевскую обувную фабрику Про Егорьевскую обувную фабрику]()
Закройщица за работой.
![Про Егорьевскую обувную фабрику Про Егорьевскую обувную фабрику]()
Согласно карте раскроя закройщица получает необходимый товар и набор резаков
![Про Егорьевскую обувную фабрику Про Егорьевскую обувную фабрику]()
Дальнейшая работа сводится к внимательному укладыванию резака под пресс. Надо экономить материал, не допуская никчёмного расходования и внимательно следить за пометками на товаре, чтобы не запустить забракованные участки в работу.
![Про Егорьевскую обувную фабрику Про Егорьевскую обувную фабрику]()
Квалификация у закройщиков разная. Самая высокая у закройщиков 6-го разряда, работающих, в основном, с дорогой хромовой кожей. Пятый разряд трудится на кожподкладке, четвёртый — на текстиле.
![Про Егорьевскую обувную фабрику Про Егорьевскую обувную фабрику]()
Искусство закройщика состоит в умении комбинировать разные детали, стремясь сократить площадь материала, уходящую на разрубы и обрезки. Отходов в обувном производстве немало. Говоря о коже, можно вывести простецкую формулу: ниже сорт кожи — больше отходов. Количество брака может составлять и 40% от площади.
![Про Егорьевскую обувную фабрику Про Егорьевскую обувную фабрику]()
Итог работы закройщика — такой комплект деталей будущего детского сапожка или ботиночка.
![Про Егорьевскую обувную фабрику Про Егорьевскую обувную фабрику]()
Чепрачная кожа. Отличается от прочих кож плотностью, толщиной и прочностью. Из неё делают подошвы детских ботиночек.
Это участок работы самых квалифицированных вырубщиков-мужчин.
![Про Егорьевскую обувную фабрику Про Егорьевскую обувную фабрику]()
Менее квалифицированный участок работы — раскрой и вырубка деталей из полушерстяной ткани. Есть ещё вырубка картонной стельки, эта операция по силам вырубщику 4-го разряда.
![Про Егорьевскую обувную фабрику Про Егорьевскую обувную фабрику]()
Вырубщик за работой.
![Про Егорьевскую обувную фабрику Про Егорьевскую обувную фабрику]()
На производстве немало иностранного оборудования: итальянского, чешского. Есть и китайское. Про китайское наладчики рассказали такое: собрано всё в «гараже или сарае», выполнено грубо, по цене доступно и работает, если доглядывать. Прогресс у китайцев в области производства промоборудования колоссальный, но культура производства пока невысока.
Осенью 1935 года в помещении бывшей фабрики-кухни города Егорьевска (Московская область) было демонтировано оборудование и начались работы по переустройству здания под промышленное предприятие. В 1936 году фабрика была принята к эксплуатации и приступила к выпуску детской обуви. Сегодня обувное производство в Егорьевске не без успеха продолжают. Всем желающим предлагается пройтись по фабричным цехам и понаблюдать за процессом создания отечественной детской обуви, выпускаемой под торговой маркой «Котофей». Автор материала Михаил Михин
Сложно сказать, с чего именно начинается производство обуви. Легко сказать без чего обувь сделать не получится вовсе: без колодок и штампов-резаков. Вот с них и начнём.
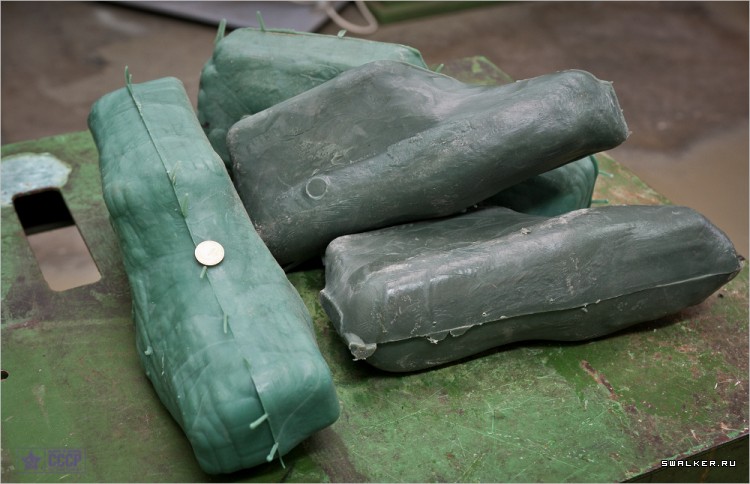
РМЦ — ремонтно-механический цех. Заготовки будущей обувной колодки. Были внезапно приняты за заготовки для деталей пулемёта РПК.
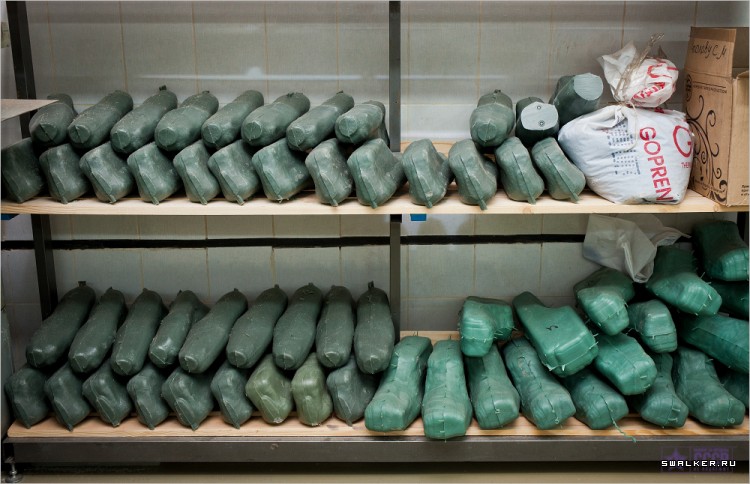
Заготовка попадает в копировальный станок.
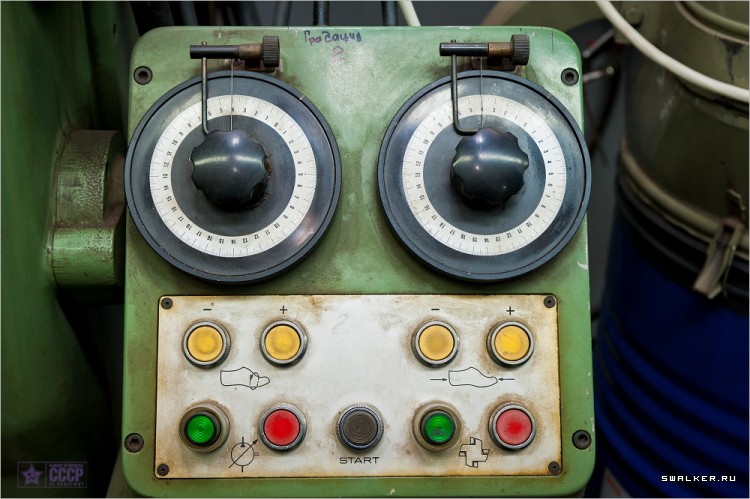
Станок вытачивает копию колодки, ориентируясь на «мастер-модель». Похожим образом в бытовых мастерских изготавливаются копии ключей.
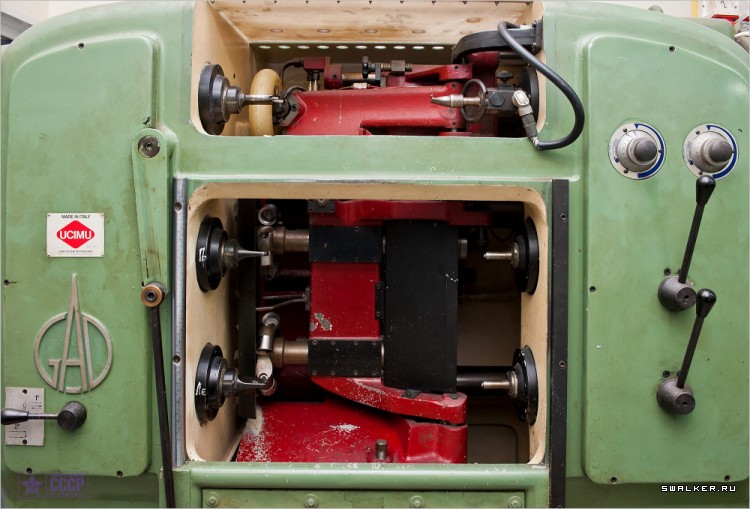
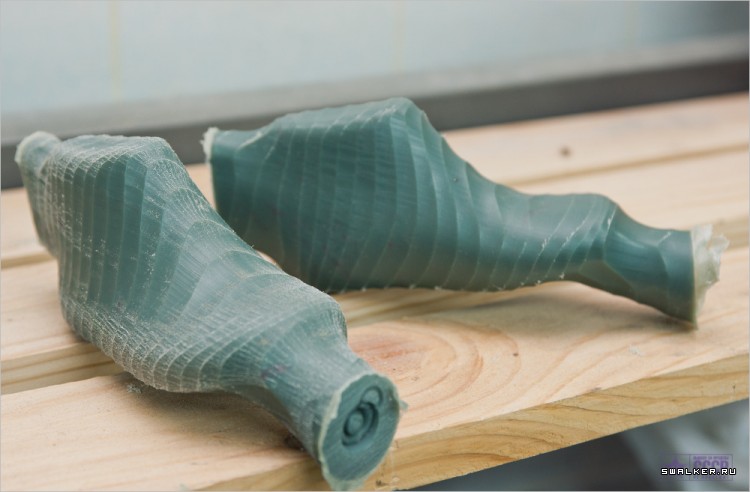
Доведённая до пригодного состояния колодка отправляется на производство.
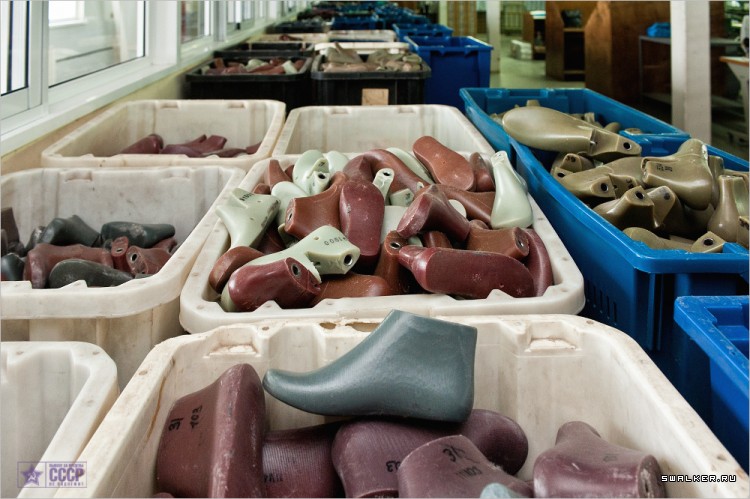
Такие колодки изготавливаются для каждого размера. Создание мастер-колодки, с которой делаются копии — высший пилотаж обувного производства. Мастер-колодочник должен учесть массу нюансов, в том числе возрастных и национальных. Русская нога — это всегда «кого надо нога». Наша национальная особенность — высокий подъём, и у детей и у взрослых. Русская детская нога пошире других, узкие европейские колодки для нас не подходят.
В середине двухтысячных на фабрике целый год велась работа по созданию новой колодки для обуви ясельной и малодетской групп. Пять сотен детей обмеряли и проанализировали итоги, собрали статистику по полноте, подъёму, высоте каблука. Новые колодки позволили начать выпуск по-настоящему удобной, эргономичной и ортопедически правильной обуви, что важно именно для растущей детской стопы.
С колодки начинается и всякая новая обувь. На этапе конструирования с колодки и присовокупленной подошвы снимается чертёж-полуразвёртка, оцифровывается и поступает в компьютер. Где обрабатывается дизайнерами и технологами в автоматизированной системе конструирования обуви. В дальнейшем тестовая модель производится в единичном экземпляре и отправляется на рассмотрение худсовета. Будучи утверждённой, модель поступает в массовое производство. На утверждённую модель создаётся модельный паспорт, где подробно и детально описывается всё, касающееся материалов и технологии производства модели.
Казалось бы, что может быть проще ботинка? Ан, нет. Не революционные, конечно, перевороты, но новые, свежие конструктивные решения постоянно находятся. А вот специалисты в этой области находятся не так часто, разрыв между наукой и производством в отечественной лёгкой промышленности растёт всё сильнее. Удивительного ничего нет: сельское хозяйство и лёгкая промышленность сейчас в категории сильно отстающих, в частности, по зарплатам. Второй непривлекательный аспект — и там и там надо работать. Такое не всем нравится.
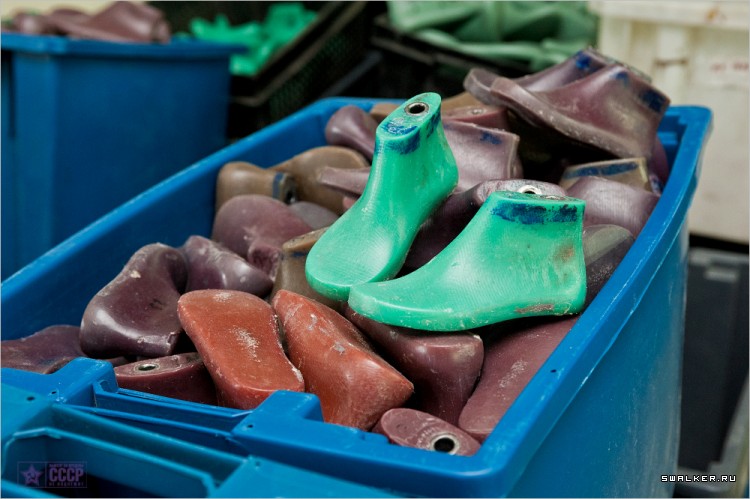
Колодка сделана, модель определена, дело за материалами.
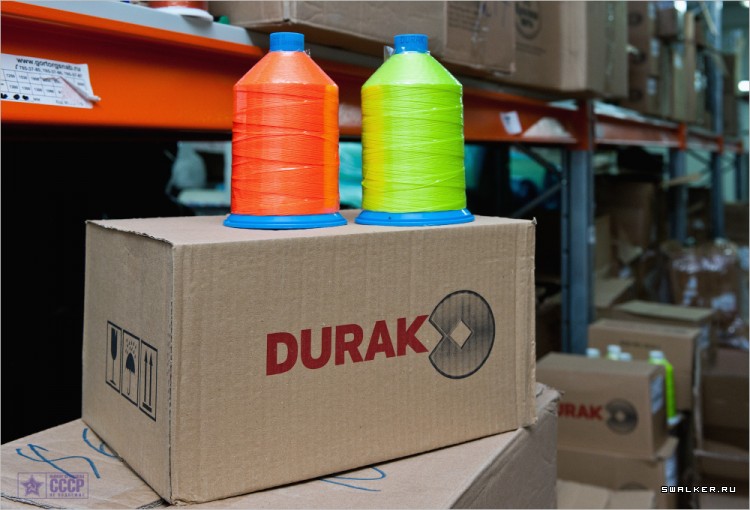
Для каждой модели технологически важно выбрать необходимые материалы. Крепкие нитки, например.
Неплохое турецкое название. Запоминающееся.
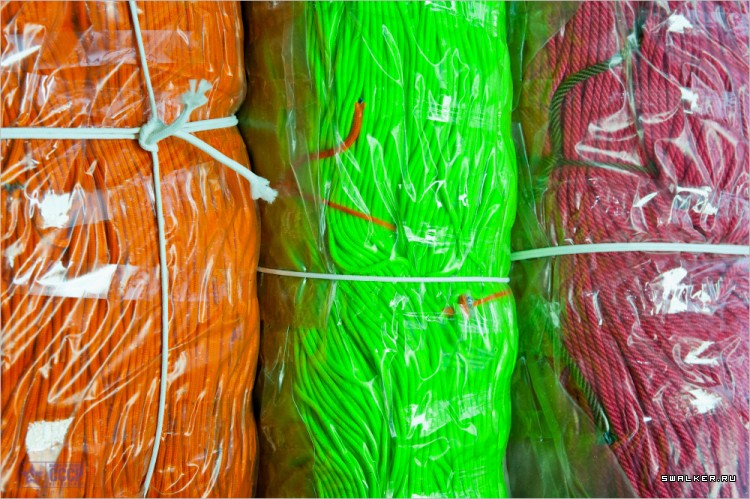
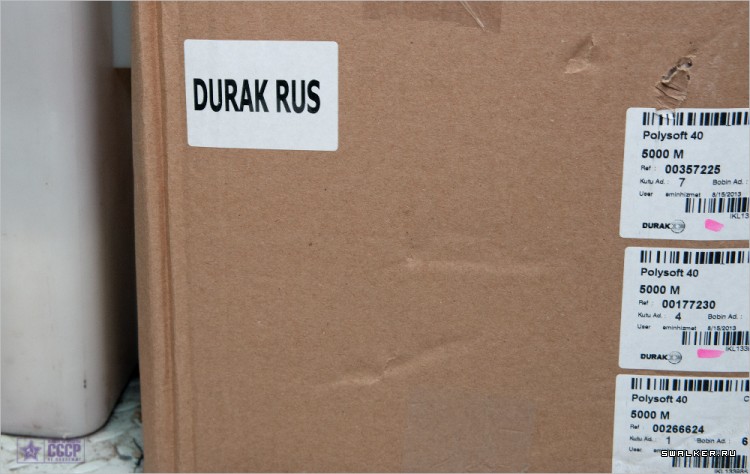
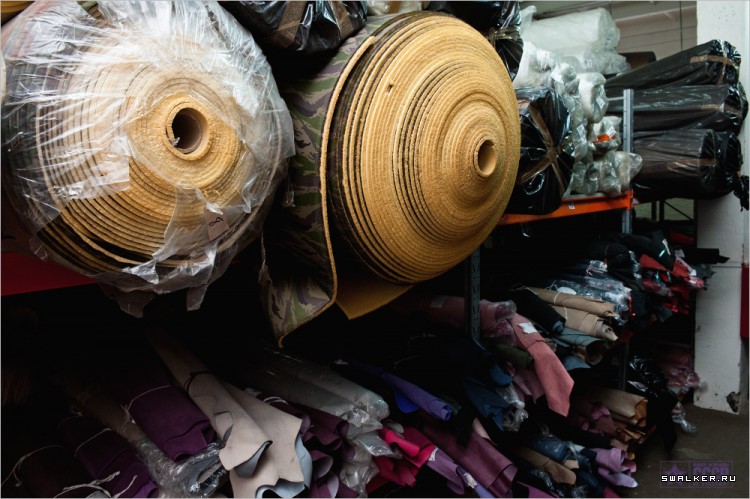
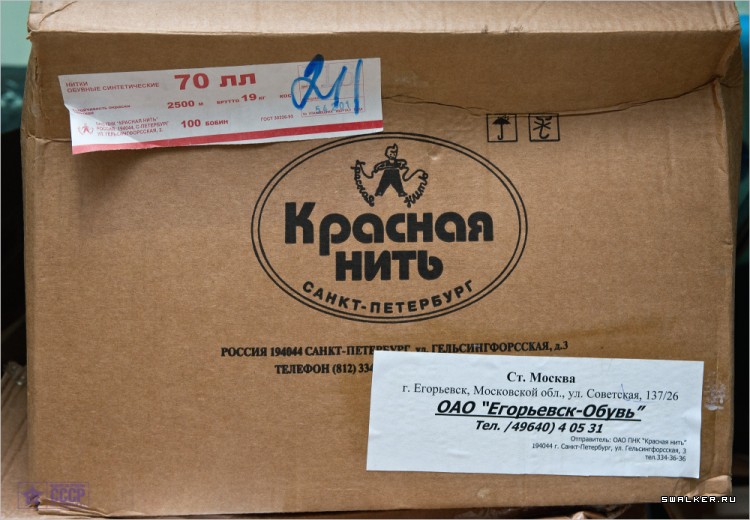
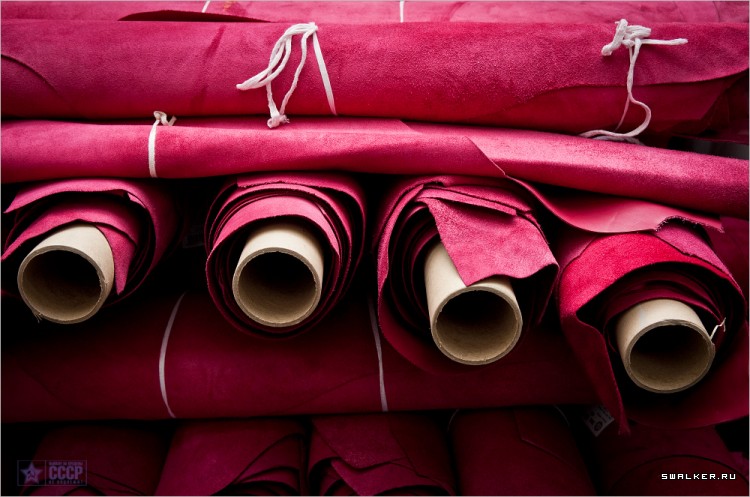
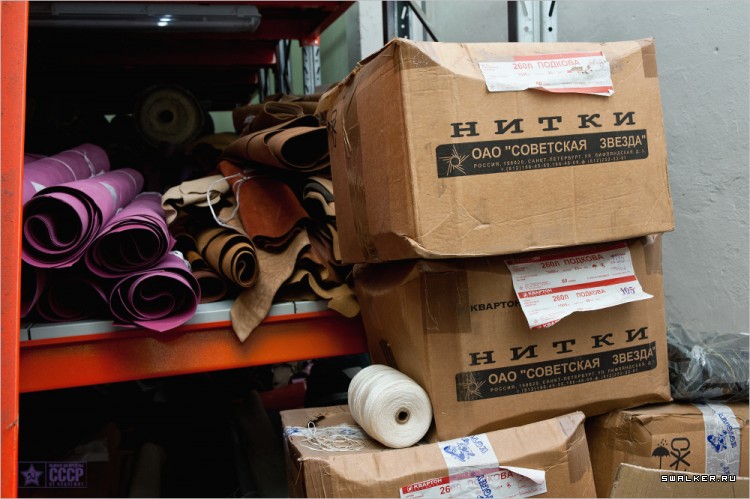
Необходимые натуральные и синтетические материалы, нитки, фурнитура — всё готово к началу производства. Но начать его без штампов нельзя.
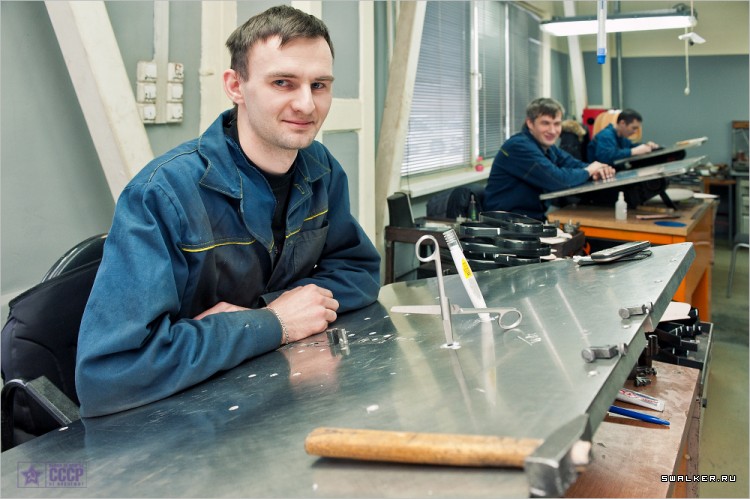
Штампы-резаки для обувной промышленности изготавливаются работниками РМЦ — ремонтно-механического цеха.
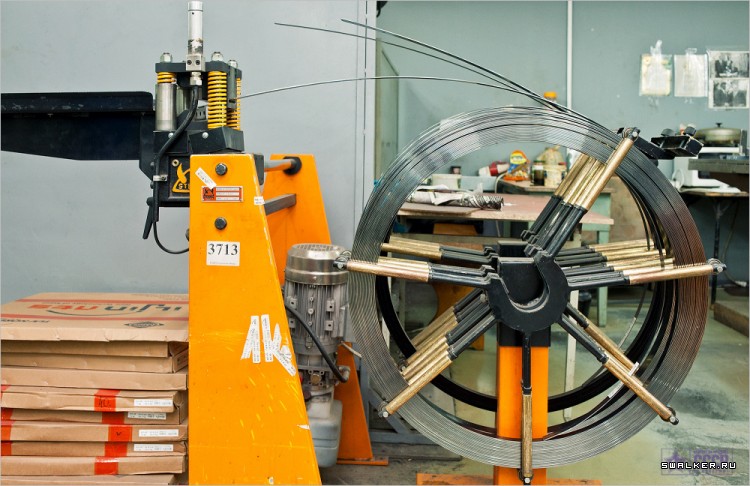
Бухта со специальной резачной сталью.
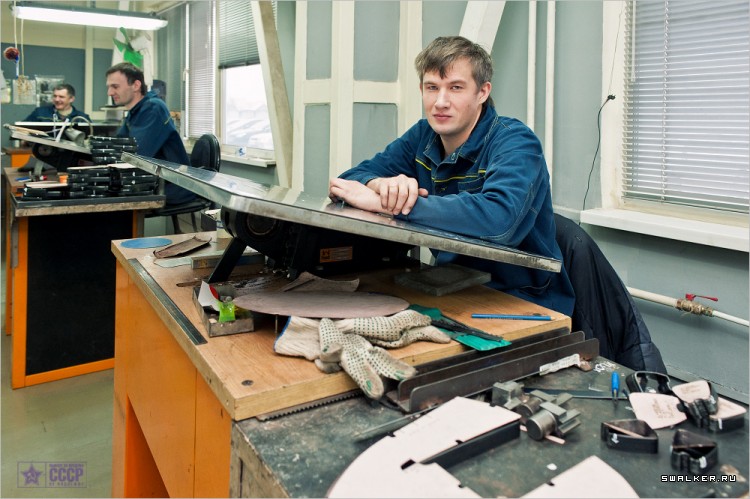
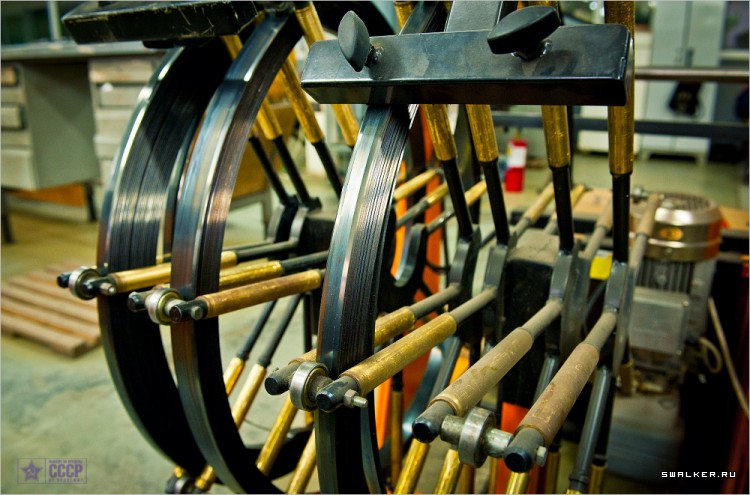
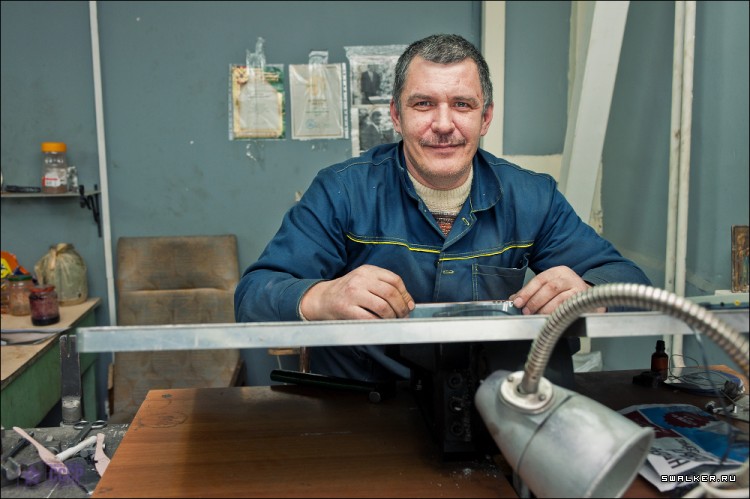
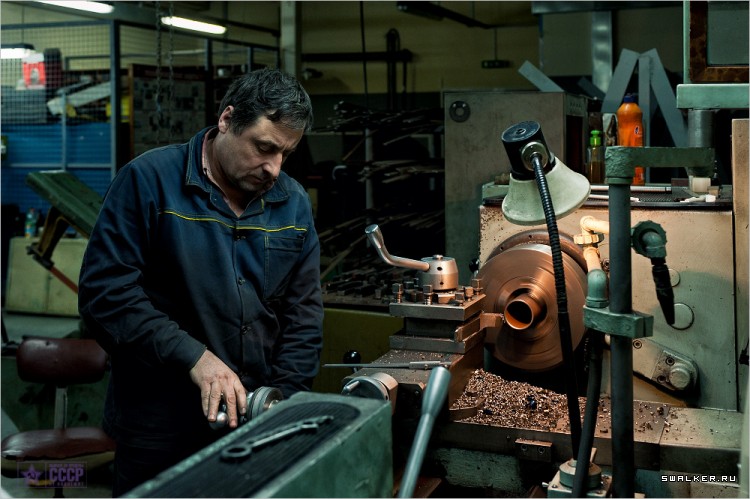
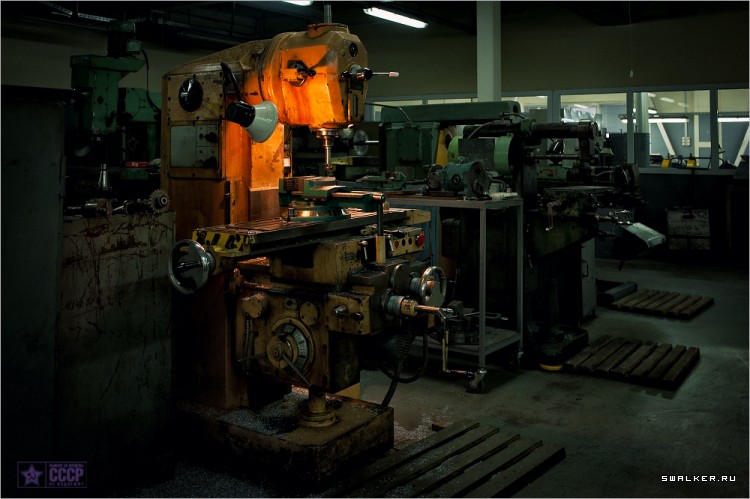
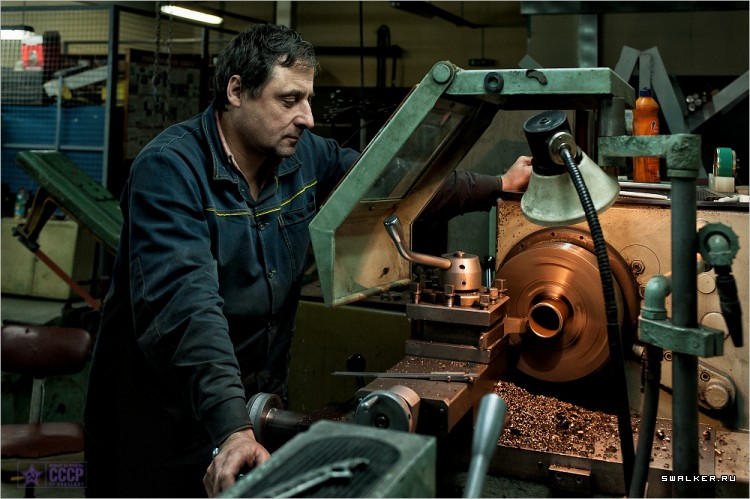
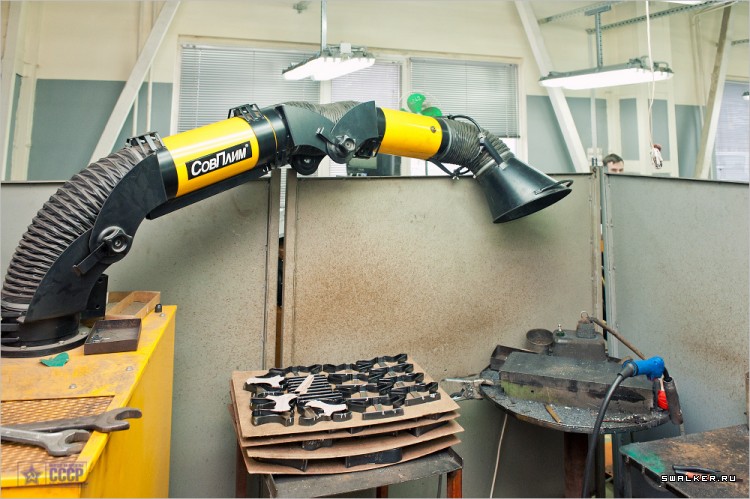
После довольно прецизионного формования будущего резака он сваривается и затачивается.
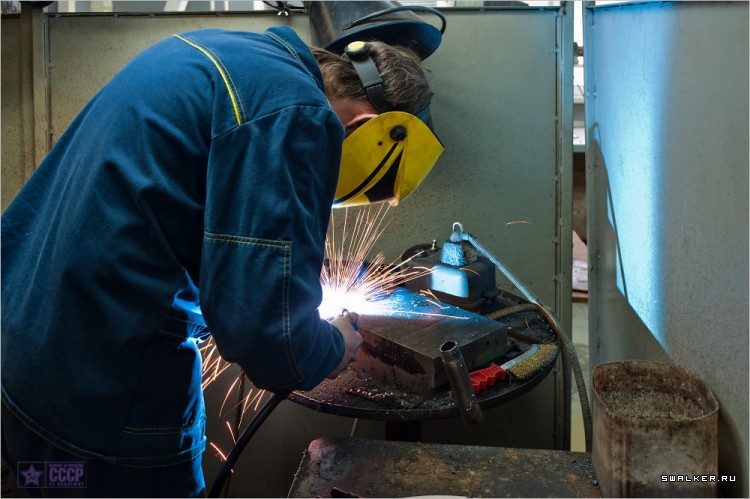
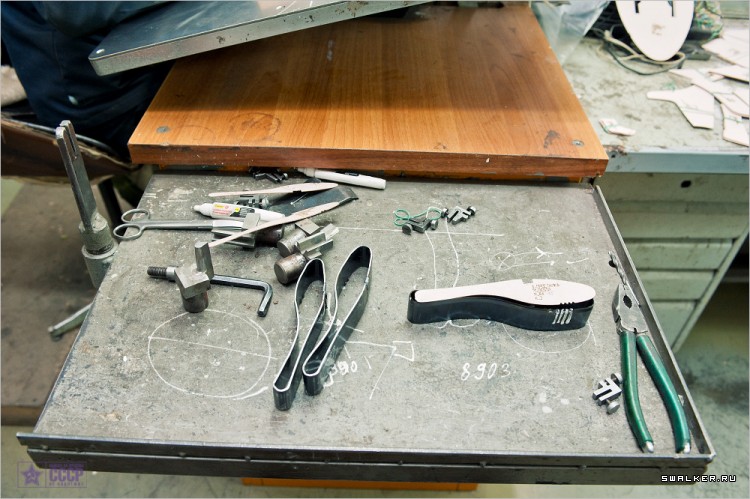
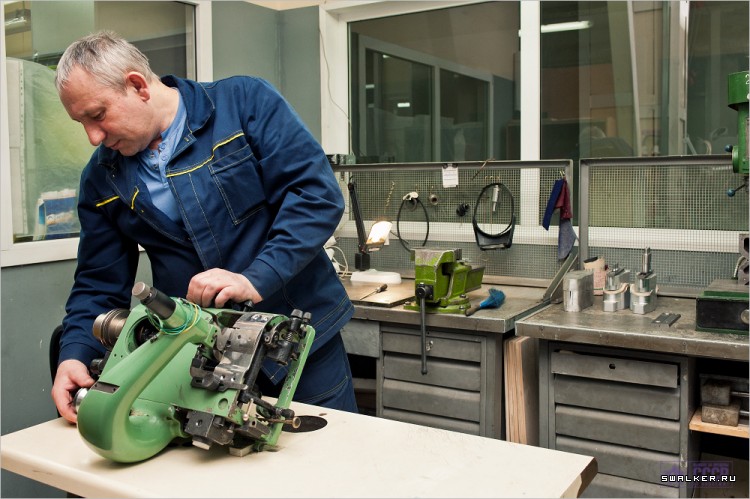
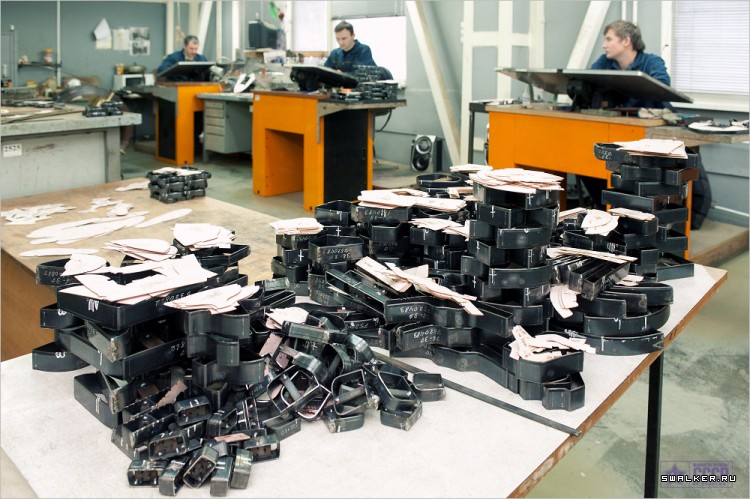
Комплект резаков для производства одной модели обуви.
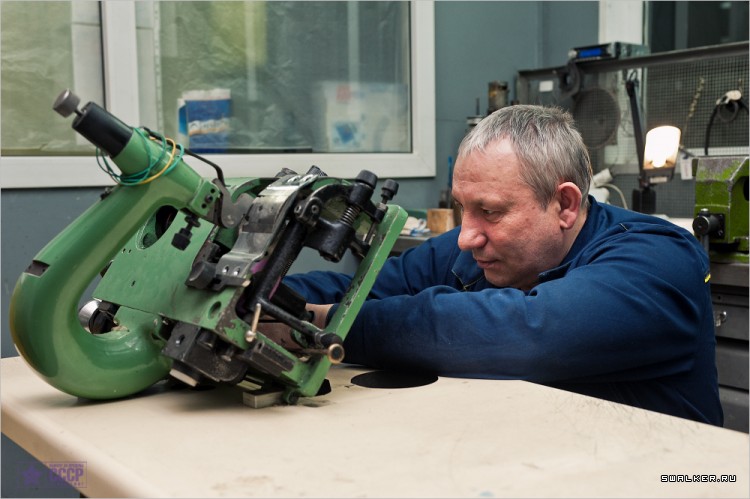
Помимо штампов-резаков, в производстве обуви применяются и более нежные инструменты.
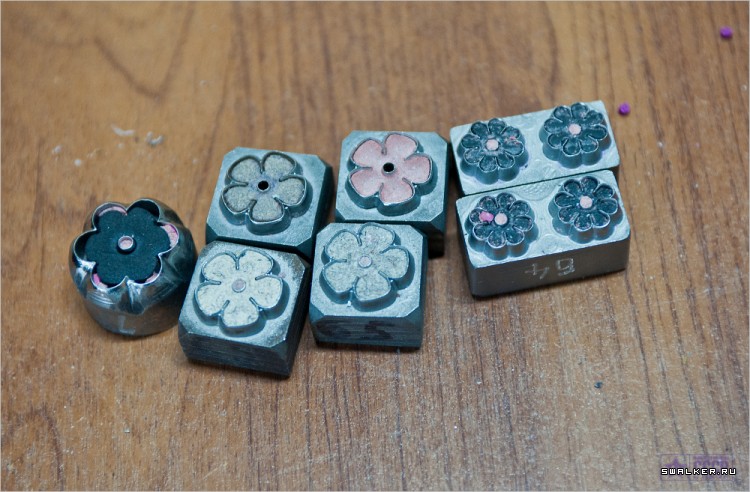
Исключительной ценности (во всех смыслах) предметы — резаки отделки. Сделаны в Италии. Каждый пронумерован. Раньше резаки на фабрике делали самостоятельно, это было и сложно и дорого. Теперь предпочитают использовать итальянские, как более качественные и доступные по цене.
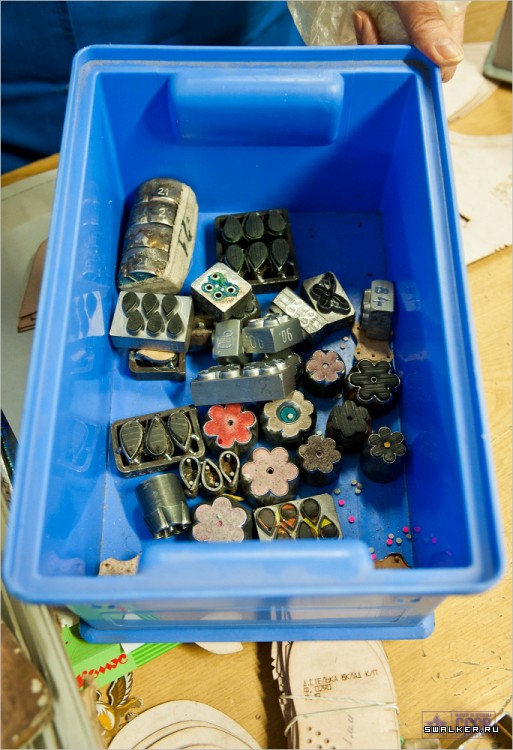
Внутри резака находится упругий материал, автоматически выталкивающий свежевырубленную деталь.
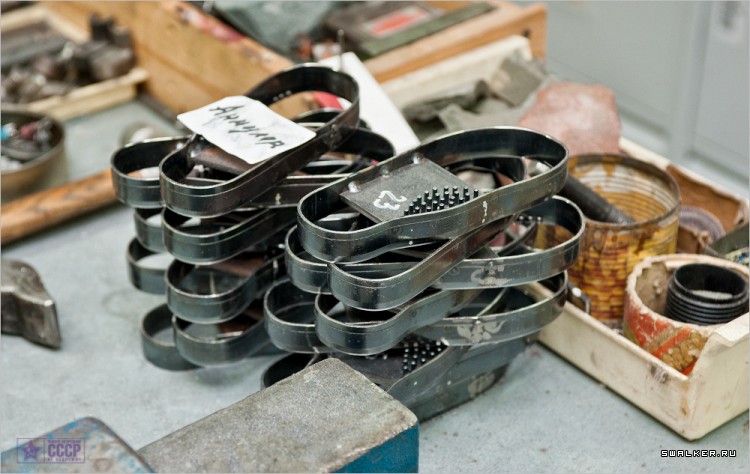
Резаки. Те самые, что поступают готовыми наборами из РМЦ. В процессе производства резаки могут подтупиться. Механики их поправят, подточат и снова вернут на производственный участок. Совсем изношенные резаки будут заменены новыми.
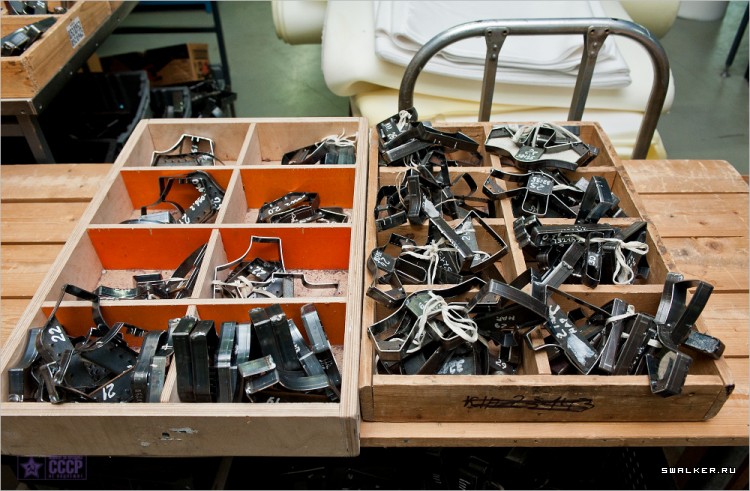
Хранят резаки в спецшкафах. На каждой ячейке указан номер модели, а специальный код разъяснит в каком ряду и на какой полке находятся резаки для данной конкретной модели.
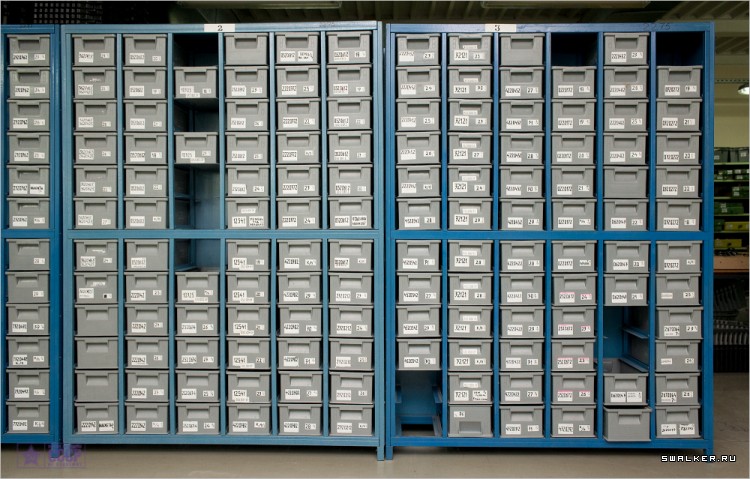
К каждому размеру каждой модели готовят свой комплект резаков.
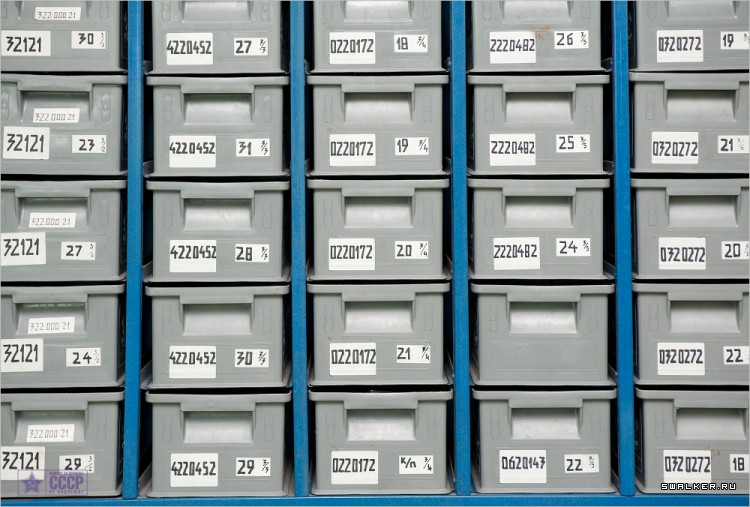
Всё это хозяйство хранится в закройно-штамповочном цеху.
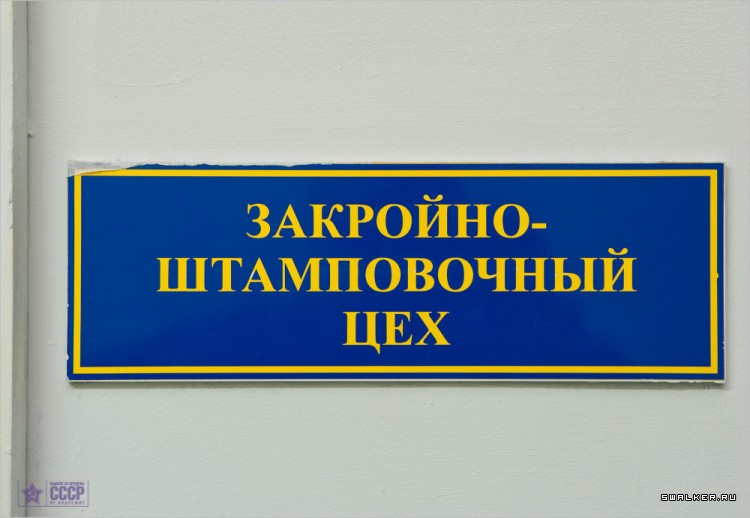
Цех состоит из двух участков: закройного (раскрой верха обуви, межподкладки и подкладки; используются кожевенные и текстильные материалы, мех, войлок) и штамповочного. На последнем производятся раскрой и обработка деталей низа. Среди таковых замечены: основная стелька, полустелька, стелечный узел (склеенные между собой стелька и полустелька) и подошва из чепрака.
Любая обувь, и взрослая и детская, состоит из приличного количества деталей. Если мысленно разобрать обычный ботинок на составляющие, то можно насчитать до 80 деталей.
Особенность производства детской обуви — исключительная требовательность к соблюдению размеров. Если на взрослой обуви погрешность в пару миллиметров может остаться незамеченной, то на детской ноге такая погрешность недопустима. Это обстоятельство учитывают везде, начиная с производства резака.
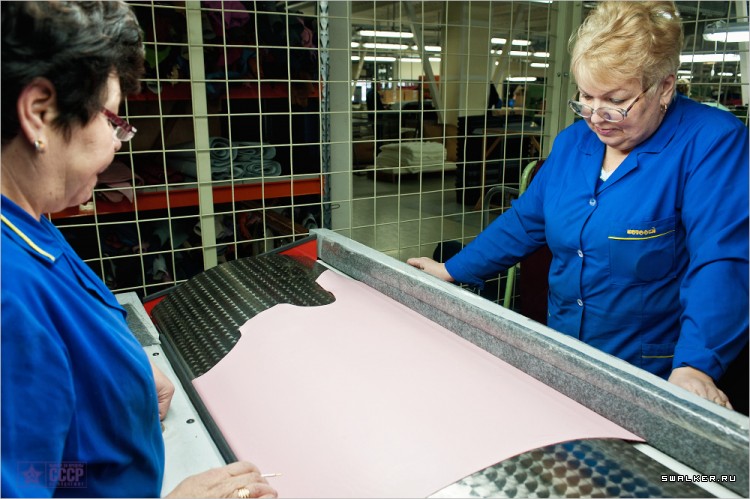
Растянутый на спецвалике материал называется термином «кожевенный товар», а среди работников именуется просто «товаром». Здесь, в самом начале производственного цикла, «товар» внимательно осматривают, помечая сомнительные в смысле качества участки каким-нибудь значком. При раскрое «товара» помеченные участки будут закройщиком опознаны как непригодные и в дело не пойдут.
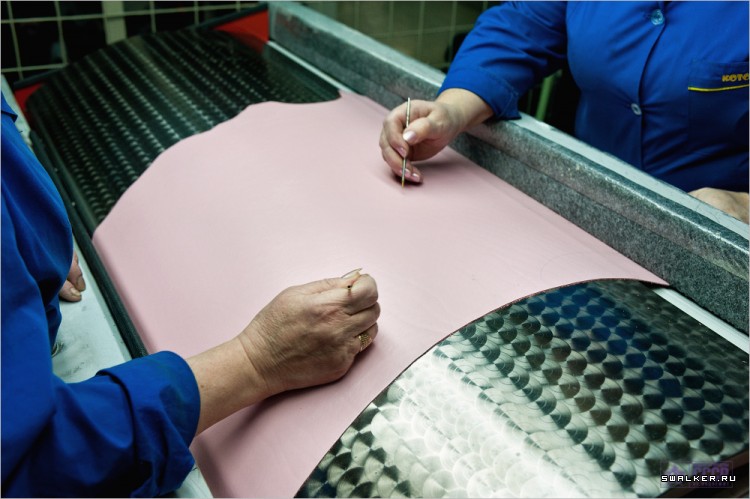
Из «товара» формируется заказ, к которому прилагается раскройная карта.
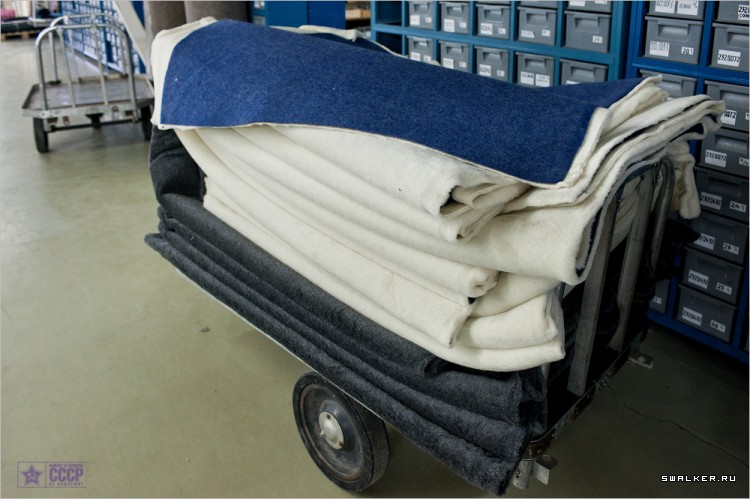
Типичный представитель «товара». Наверху наш, отечественный войлок. Ниже китайская ткань, в самом низу совместное российско-итальянское творчество. Отечественных материалов в обувном производстве немного. Российские поставщики сырья, в лучшем случае, остановились в технологическом развитии на уровне позднего СССР, а в худшем вовсе прекратили своё существование.
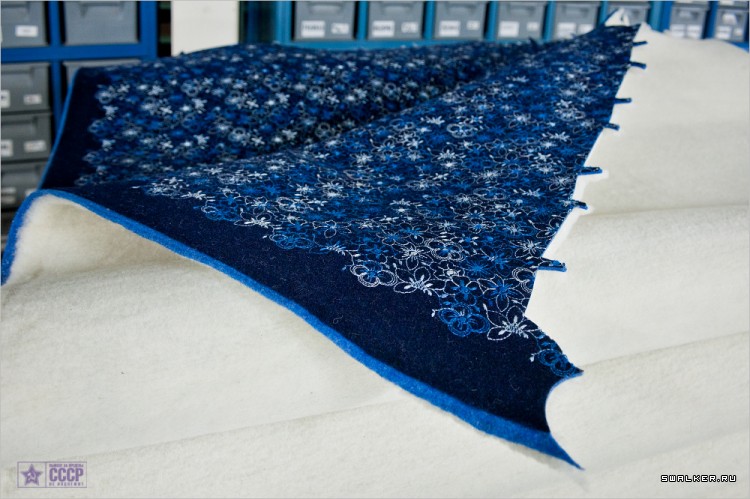
Это итальянский войлок. Красивый внешне и дублированный мехом изнутри. По качеству наш войлок лучше, плотнее. Итальянский заметно рыхлее, хуже теплоизолирует, зато выглядит наряднее. Приходится либо дополнительно украшать наше сырьё, либо использовать итальянский товар, привлекательный прямо из рулона. Такая же петрушка и с фурнитурой: отечественных комплектующих мало или нет совсем, приходится закупать иностранные. Хотя фурнитуру можно производить и самостоятельно, это совсем не rocket science.
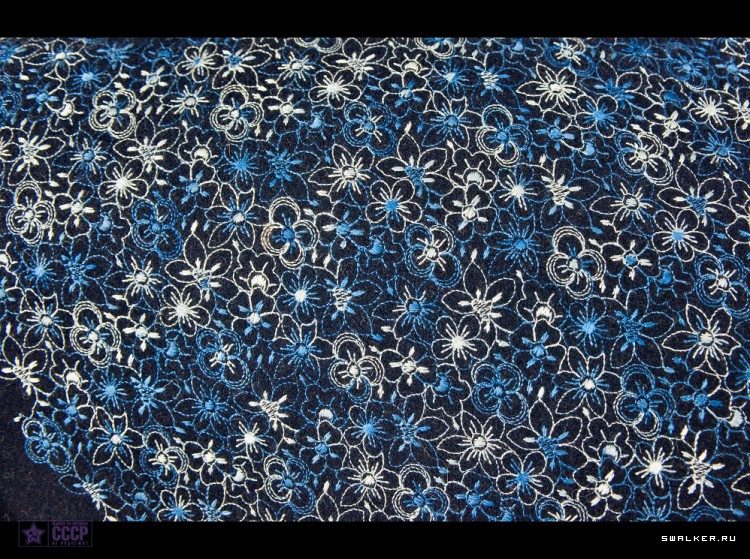
Интересная ситуация складывается с кожсырьём. Выгодно проделать разного рода «грязные» операции по первичной обработке кожи здесь, потом отправить её за рубеж, там отделать и продать по совсем уже другой цене обратно.
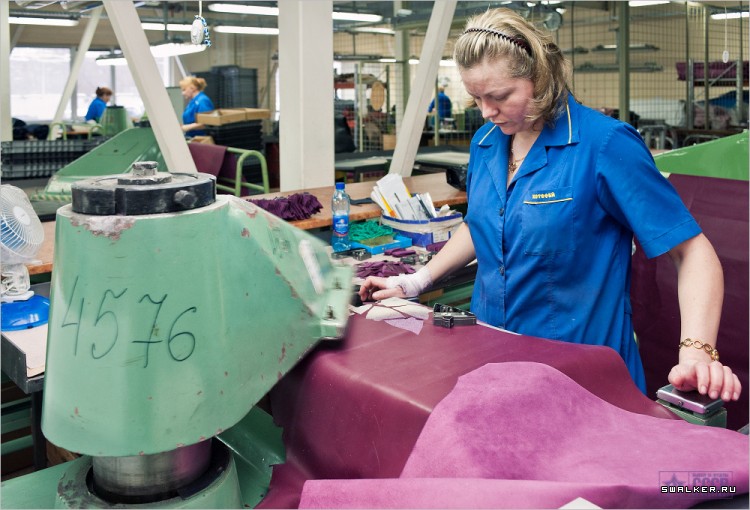
Закройщица за работой.
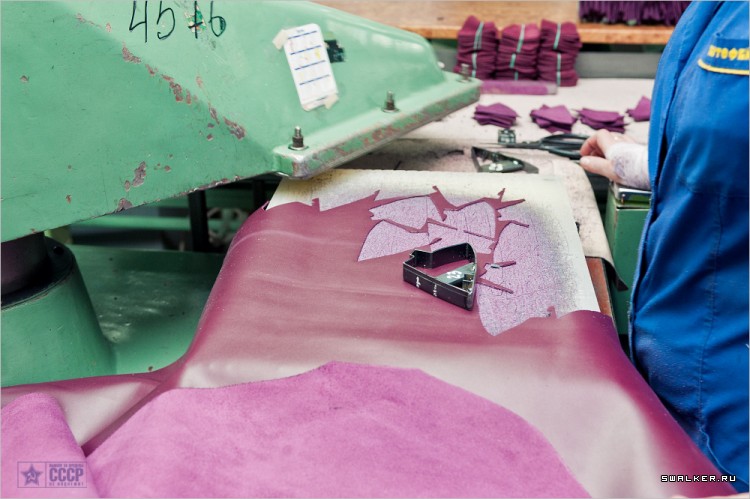
Согласно карте раскроя закройщица получает необходимый товар и набор резаков
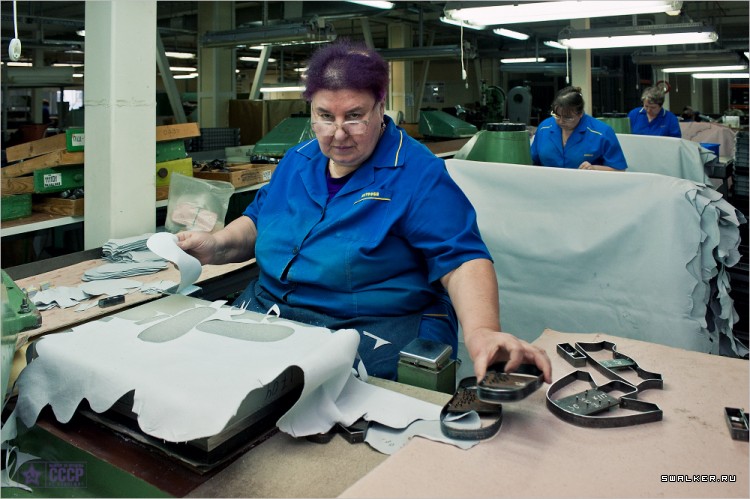
Дальнейшая работа сводится к внимательному укладыванию резака под пресс. Надо экономить материал, не допуская никчёмного расходования и внимательно следить за пометками на товаре, чтобы не запустить забракованные участки в работу.
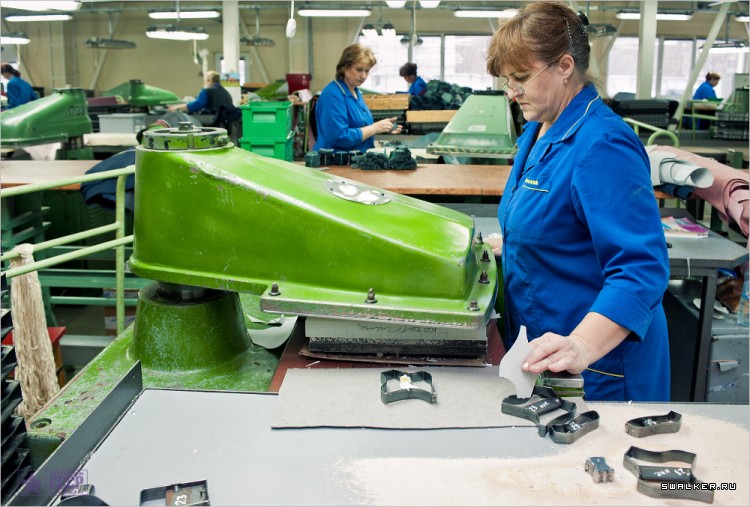
Квалификация у закройщиков разная. Самая высокая у закройщиков 6-го разряда, работающих, в основном, с дорогой хромовой кожей. Пятый разряд трудится на кожподкладке, четвёртый — на текстиле.
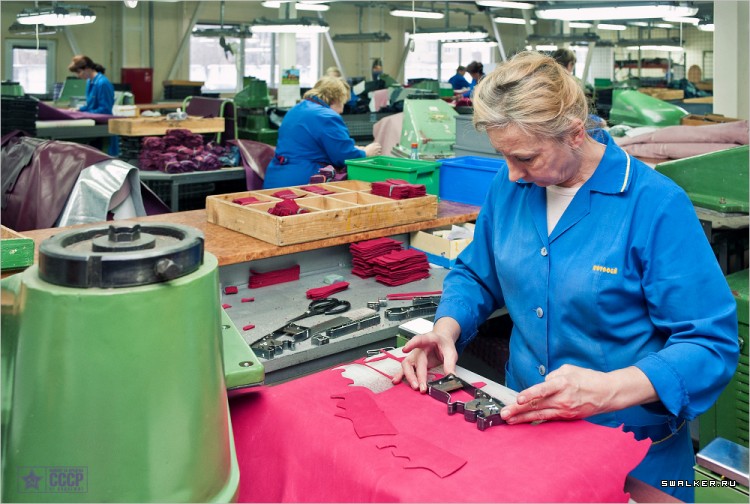
Искусство закройщика состоит в умении комбинировать разные детали, стремясь сократить площадь материала, уходящую на разрубы и обрезки. Отходов в обувном производстве немало. Говоря о коже, можно вывести простецкую формулу: ниже сорт кожи — больше отходов. Количество брака может составлять и 40% от площади.
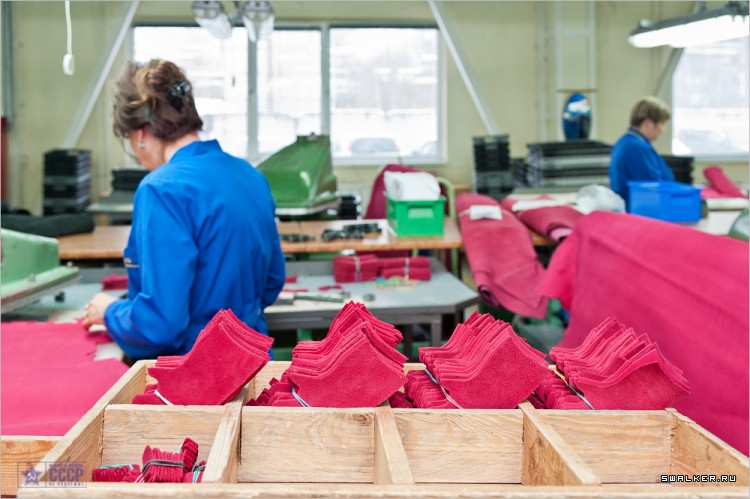
Итог работы закройщика — такой комплект деталей будущего детского сапожка или ботиночка.
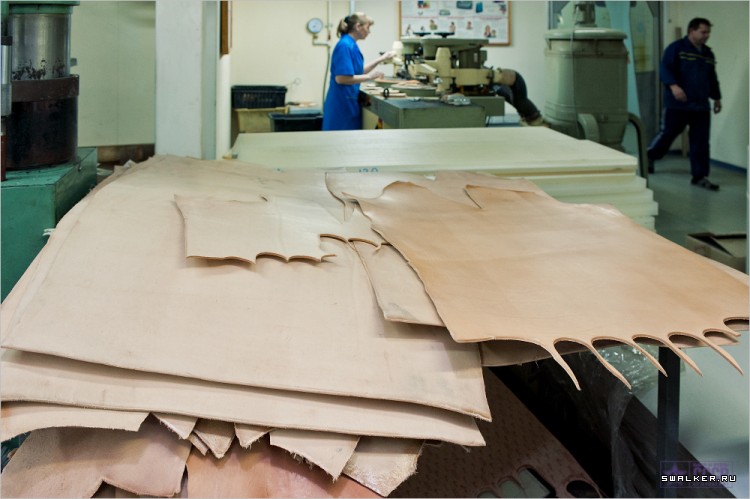
Чепрачная кожа. Отличается от прочих кож плотностью, толщиной и прочностью. Из неё делают подошвы детских ботиночек.
Это участок работы самых квалифицированных вырубщиков-мужчин.
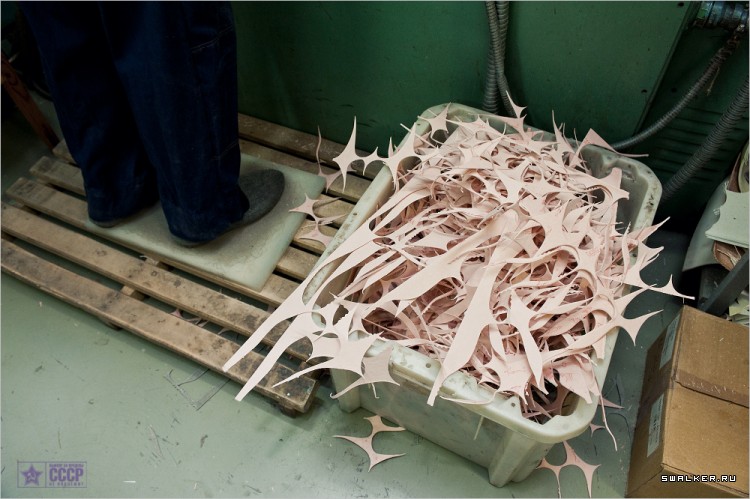
Менее квалифицированный участок работы — раскрой и вырубка деталей из полушерстяной ткани. Есть ещё вырубка картонной стельки, эта операция по силам вырубщику 4-го разряда.
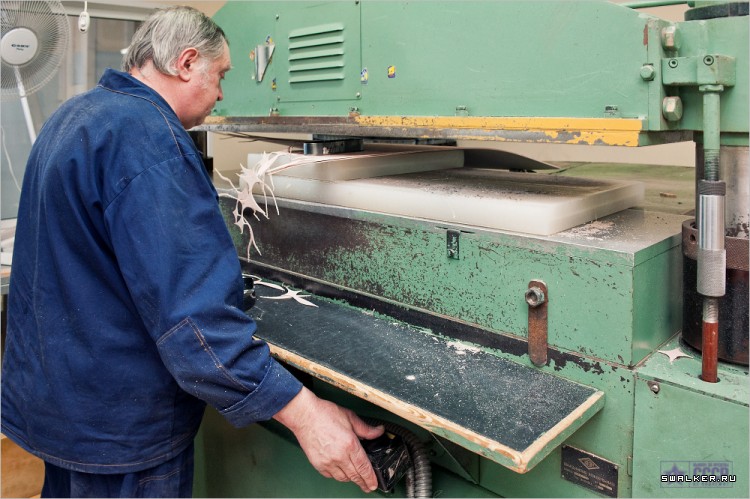
Вырубщик за работой.
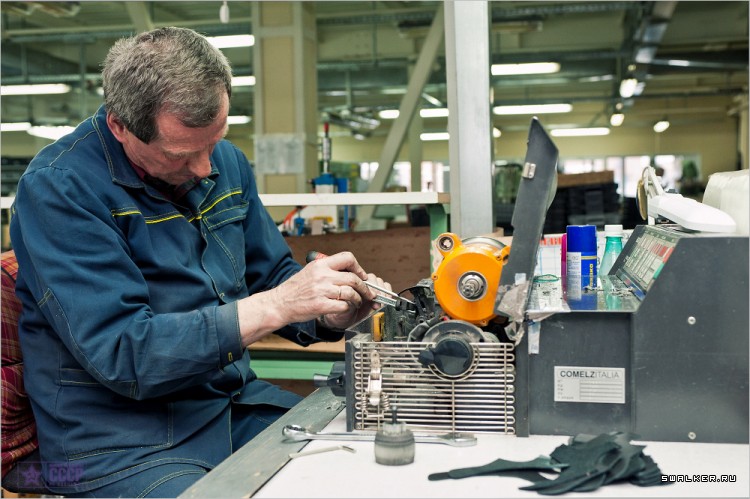
На производстве немало иностранного оборудования: итальянского, чешского. Есть и китайское. Про китайское наладчики рассказали такое: собрано всё в «гараже или сарае», выполнено грубо, по цене доступно и работает, если доглядывать. Прогресс у китайцев в области производства промоборудования колоссальный, но культура производства пока невысока.
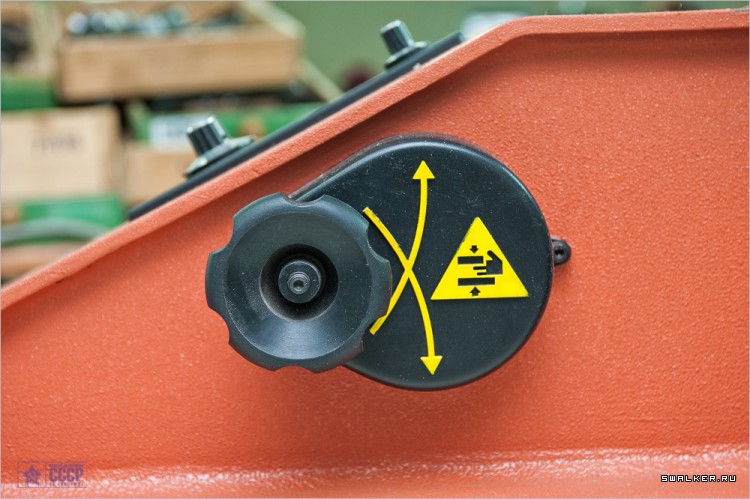
Комментарии - всего 4